Monday, 10/06/2024, 09:44
(is Hackaday.io going down to all of you or just me? Some times I need to wait an entire day for the website to be accessible)
Well, I feel like it is a bit too soon to be worrying about design, and specially since I literally didn't start working on it at all even though I name the project logs exactly to do that. :|
But here we go again with my shenanigans...
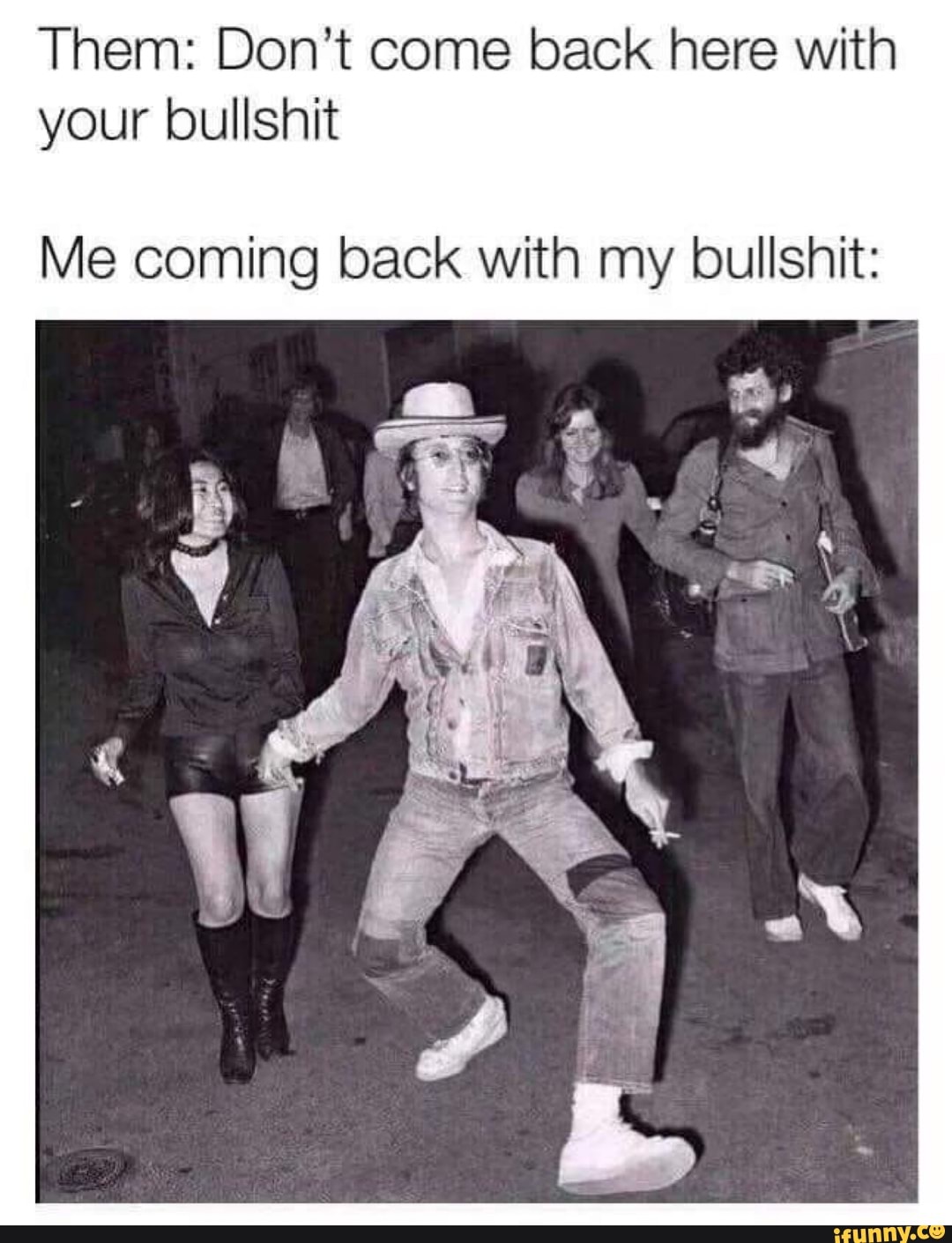
Design of the Artificial muscles:
Materials for dielectric elastomers:
Well, since I'm intending on making dielectric elastomer fibers with 1mm of thickness, I can't really just make it whatever way I want and leave at it.
I could simply connect a single fiber and be done, since very high voltages and very low amperages can travel kilometers in materials without any loss, but if any fiber is damaged, well, you could have the entire thing stop working. Of course, I still could make the fibers slightly bigger and just connect new muscles whenever some fiber is damaged, and I do intend on doing that if this idea shows itself to not be viable.
(I want to make it as small as possible because I'm afraid that the contraction ratio of the muscle will force me to change the proportions, right now the idea is that the muscle is attached to 1/3 of the limbs length, if I'm reguired to increase it, then it would make the muscles even heavier)
I need polymers that are soluale in a material, but not in other. At least for the outside layer.
Polyvinyl alcohol is soluable in water and alcohol, but not in acetone or gasoline.
Polystyrene (styrofoam) is soluable in acetone and gasoline, but not in alcohol or water. (Funnily enough, polystyrene is even cheaper than PVA)
Poly(methyl methacrylate) (PMMA) is soluable in acetone, but not in alcohol, water or gasoline.
Polyvinyl chloride (PVC) is soluable in acetone, but not in alcohol, water or gasoline.
So, if my brain isn't being stupid: for half of the outer layer of PVC/PMMA that dissolve in acetone and for another half, I would need a material that dissolves in gasoline, but not in acetone, alcohol or water. I could only find a few forum questions saying that PET and LDPE can be damaged by gasoline over time, but not something that can actually dissolve.
I found out that if I mix PVA with dielectric silicone grease, it becomes resistant to water, but also that there are waterproof PVA glues in the market. So I "just" need to mix it with PVA and make it hydrophobic.
So, the design of the actuator:
Outer layer of negative electrode side = Dielectric Soluble Polymer 1 + low friction material + other additvies if required. |
Negative Compliant Electrode = fumed silica powder + graphene + polymer. |
Dielectric Elastomer Layer = Dielectric Elastomer Polymer + titanium dioxide + other additives if required. |
Positive Compliant Electrode = fumed silica powder + graphene + polymer. |
Outer layer of positive electrode side = Dielectric soluble Polymer 2 + low friction material + other additvies if required. |
I don't know what polymer to use on the electrodes yet, I was thinking on just using PVA. I also don't know which low friction material I should use for the outer layers, I was thinking that they should have low friction for better actuation of the artificial muscles...
So the idea is to:
- Make a 1 mm (less or more) fiber with this structure.
- when deciding to attach to a limb, over the attachment places of the skeleton/limb with dielectric material.
- Roll the dielectric elastomers up in a loop.
- Hold them in place with a really tight cable.
- Making the "tendons" by going with another rope through the loops.
- Use one solvent in one tip of the muscles and the other solvent in the other tip.
- Cover the tips in a conductive polymer (probably PVA) with the negative and positive electrodes.
- Connect everything to the electronic system.
- Then wrap everything in another layer of dielectric material to avoid the electrical current to arc.
- Done.
- Optional: I also thought on surrounding the muscles with a plastic bag and fill it up with a dielectric liquid, grease or gel for extra safety if any fiber muscle comes to be damaged.
"Just" that, god, I whish there was an electric artificial muscle that didn't need a positive and negative end...
You could just have a dielectric elastomer in which you just insert the electricity, but doesn't need the other electrode to be connected to anything, the difference in energy potential alone would make the dielectric elastomer actuate. However, I do think that the difference in voltage of the powersource is bigger than the difference in voltage of the material alone. But I don't know who to ask.
For some reason I can't find the goddang dielectric values of polyvinyl alcohol, it is said it is high, but never how much.
And I'm not talking about dielectric constant, but dielectric strength and breakdown voltage.
Well, after 2 hours I actually found it, in this paper it says that:
"The dielectric strength of polyvinyl alcohol (PVA) is potentially very high i.e >1000 kV/mm. "
Ok... But I think that using cheap off-the-shelf PVA glue with waterproof PVA glue mix won't give such insane results, I guess that I will literally need to buy the equipment and test it to failure...
Now I need to find out how to make a power source that reaches high values of Kilovolts and high values of Hertz...
Actually, I found power supplies like that, but they cost thousands of bucks, so I will need to build everything homemade, which I'm not capable right now since I bought a new table and a new drawing tablet...
Just now GPT actually answered me other materials that actually are soluable in different solvents than PVA and Polystyrene.
Like Polyoxymethylene (POM) or Polyacetal that aren't soluable in acetone nor water or alcohol, but it is soluable in Benzyl Alcohol, but although I couldn't find how it affects PVA and Polystyrene, it probably dissolves one of them.
In any case, I will keep trying to find new options.
On a side note, the dielectric constant is the value of how much charge a given material can store, so the higher the dielectric constant, the higher the energy density of the material.
HOWEVER, this can also decreases its breakdown voltage (depending on the material), so you can't just take a material that has insane high dielectric breakdown voltage if it can't store that much charge...
So, making a list:
I will make it later, right now I'm reading manga, lol
The manga is a generic tutor isekai crap, it is not that big of a deal, I just like to read something silly and dumb to forget a little about our burning world full of horros beyond our comprehension.
Now I finished it:
Name (for some reason this part of the table is squished): | Dissolves in: | Insoluble in (for some reason this part of the table is squished): | Dielectric Breakdown Voltage: | Dielectric Constant (it can change severely based on hertz): | Tensile strength: |
Polyvinyl Alcohol | Water, Ethanol | Acetone | 45 (source), 420 (source) to 1000 (source) KV/mm | 1.01 | 8-40 MPa depending on the source. |
Polystyrene | Acetone, Gasoline | Water, Ethanol | 24, 25, 400–600 KV/mm | 2.6 | 5-50 MPa |
Polyoxymethylene (POM) or Polyacetal | Benzyl Alcohol | Water, Ethanol, Acetone | 19.5 to 50 KV/mm | 3.02 | 69 MPa |
Titanium dioxide | Not required | Not required | 12-270 KV/mm (Depending on the source 1, 2) | 85-173 | Not required |
Aluminium Oxide/alumina | not required | not required | 14 KV/mm (source) | 8.6-10 | not required |
FiberGlass | Not required | not required | 2,000 KV/mm | 6.2 | not required |
Silicone Rubber | Acetone, Mineral spirits, tuolene, white vinegar, Isopropyl Alcohol, Methyl Ethyl Ketone (MEK) | Water, Ethanol | 39.5 KV/mm | 3 | 3-5 MPa |
Dielectric Silicone Grease | Same ones | Same ones | 0.350-1.5 KV/mm | 2.6-2.9 | Not required |
Polyurethane rubber | Acetone, toluene, xylene or MEK | Water, Ethanol | 70-90 KV/mm | 13.5 | 3-5 MPa |
Polyethylene (HDPE/LDPE etc) | Tuolene, Xylene | Water, Ethanol, Acetone | 50, 500–700, 18 KV/mm | 2.2 | 20-45 MPa |
Polypropylene | Xylene, Tetralin and Decalin | Water, Ethanol, Acetone | 30-40 KV/mm | 2.1 | 30-45 MPa |
ABS | Ester, Acetone, Chloroform | Water, Ethanol | 20-25 KV/mm | 20-25 | 30-60 MPa |
Nylon | Phenols, calcium chloride-saturated methanol solution and concentrated formic acid | Water, Ethanol, Acetone | 25 KV/mm | 3.5 | 85 MPa |
Polycarbonate | Ethylene chloride, chloroform, tetrachloroethane, m-cresol, and pyridine | Water, ethanol, acetone | 15-67 KV/mm | 2.9 | 39-120 MPa |
Teflon | Virtually none | Virtually all | 60 KV/mm | 2.05 | 41 MPa |
Lead zirconate titanate | not required | not required | 25 KV/mm | 500-6000 | Not required |
Talc Powder | not required | not required | 200-500 KV/mm | 3-15 | not required |
Cellulose Acetate | acetone, spirits and ethanol. | water | 11-15 KV/mm | 3.6 | 26-33 MPa |
Polyvinyl Acetate | acetone, spirits and ethanol. | water | (not found) | 3-15 | 3-10 MPa |
Now that I finally finished the list I end up finding this PDF archive that pretty much lists all of the polymers out there... There is also this textbook and this one.
There is also this list of the highest dielectric constant (aka permitivity) materials.
Funnily enough, I could find Lead-Zirconate-Titanate piezoelectric devices in a reasonable price on aliexpress. Even if I bought them and broke them back to powder, I don't know how much of their original properties would be left...
I also thought on adding diamond powder to the composite of the dielectric layer, since it has such high breakdown voltage. But I don't know if the diamond powders out there are really diamond or just zirconia.
Well then... I've made this huge list, now what?
Hum...
First:
maybe the 1mm thick fibers aren't a realistic goal for this project, maybe I should aim for a dielectric elastomer layer with 1mm of thickness.
Second:
I need to find a way of making the restrained DEA with the mesh, I mean, I don't know how to mass-produce at home these braided mesh for a 1mm of thickness dielectric elastomer actuator.
I also don't know if other shapes could work, for example, the McKibben muscle works in a similar way with the braided mesh, but they also use linear meshes. If the linear meshes are viable, then would them work in the fiber 3D printed DEA?
Restricted DEA with a braided mesh:
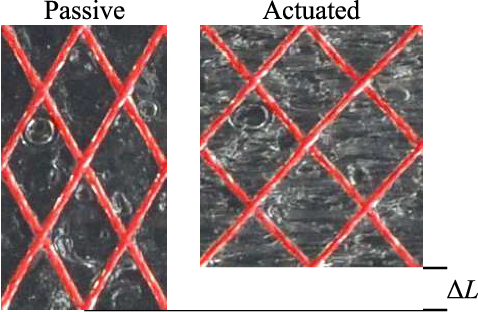
McKibben muscle with a similar mesh:
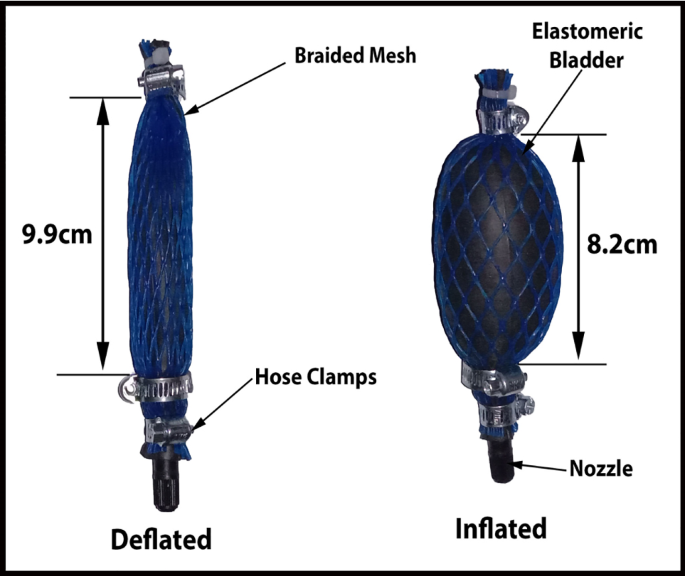
McKibben muscle with linear mesh:
Would any of these work with the fibrous 3d printed DEA?

If this was to work, then it woud way easier to make the actuator in a mass-produced manner, and it would probably be possible to make it smaller than 1mm.
Although the dissolving the opposite electrodes idea will be in the trashcan after this... Or maybe not, the image shows that you could print the fibers without one of the electrodes, so every X meters I would go switching which electrode can be accessed by simply not printing one of the four parts (outer dielectric layer > outer electrode > Inner dielectric layer > inner electrode)
Also, I was considering making the electrodes liquid (or even a gel), so it would be easier to simply remove the extra fluid of one of the concentric tubes. Some even use room temperature liquid metals like galinstan.
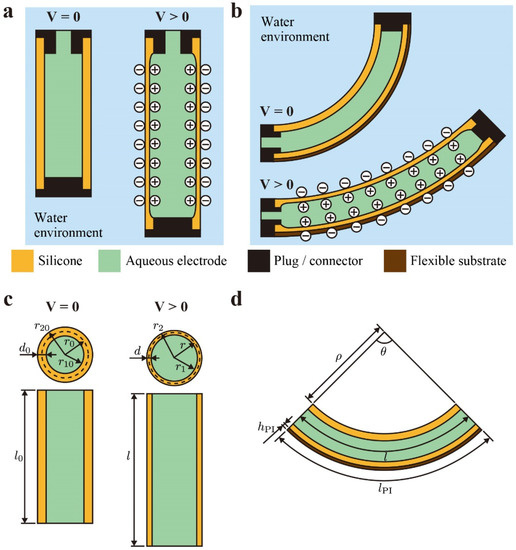
Source: https://www.mdpi.com/2073-4360/13/24/4310
The use of liquid electrodes also doesn't solve the problem that I would need to connect thousands of fibers, I really need to solve this problem, even if it where the conventional sandwich of dielectric elastomer layers, it would still be a problem to wire thousands of fibers.
Just now I remembered that there is the option of a spiral fiber dielectric elastomer actuator:

Maybe with this design I could turn the inner hole a continuous connector and the outer tube also a continuous connector, let's say, you can only access the negative electrode from the outside and the positive through the inner side. Although... I still don't know how well this would work... I can still use the idea of covering the different electrodes with different plastics that dissolve in different solvents.
There is also this design:

I know that I simply never stop adding more and more designs that could pottentially work, but I do think this is it. This one allows the fibers to be actually around 1mm to 2mm thick while also allowing the separation between the electrodes to be also 1mm without making the electrodes too thick.
My only gripe with this design is that the center contracts more than the borders, so how exactly would it reduce its length if the entire border of the actuator is connected to something?
The only reference I have are these two videos of dielectric elastomer actuators:
The first is just like the 3 dimensional version of this planar electrode, while the second doesn’t seem to have the same issue because it doesn’t seem to have the outside electrodes.
The only problem remaining is that I kinda want to use PVA because of its price, but there isn't anything that doesn't dissolves in something PVA does… I guess that I could simply mix it with waterproof PVAc (wood glue) to make the core water-proof but not the electrode protection, or even hydrophobic materials like fumed silica.
So, a drawing of how I intend on doing it:

Obviously, this will be a continiously printed dielectric elastomer actuator.
Also, I didn't talk about it because I didn't want to bloat the project log more than it already is, but taking into consideration the thickness of everything, a lot of these options for fiber DEA's ended up being half a centimeter of thickness (or even wider) when you stop to think its dimensions. Besides, I do think this version would also be easier to print without some crazy DIY setup. I could even use a rolling printer for this.
Oh yeah, I forgot to write about the efficiency of dielectric elastomer actuators. They work through the Maxwell stress, so a lot of energy is wasted just to overcome the resistance of the material for bending. So, the efficiency is around 18%-20% and maximum 60% while recycling the energy that comes out of the muscle, they are a kind of capacitor anyway.
Okay guys, this is the last time, I swear.
I'm not satisfied with the hypothetical performance of this dielectric elastomer, I'm not very confident on its actuation strain and efficiency. And after some consideration, I do believe that the best material to continue with this endeavour is the HASEL actuator. They don't neeed an elastomeric material, only a flexible one.
They can also be tuned to have higher contraction ratios as shown in the video.
I also tried to find a dielectric elastomer and HASEL hybrid only for the sake of not throwing the design away, but I couldn't find any.
And finally, I will need to figure out how to extrude this thing. I was thinking of even using a 3D printer… Initially I was against the idea because I was thinking of making everything as thin as possible, since this is not the objective anymore, dimensions of millimeters are really within any 3D printer. After all, 3D printers have a precision of 0.2mm or even smaller. And for that I would need multiple nozzles and a multi-material screw extruder for mixing all the materials together.
And at this point, I’m not even sure if I will use PVA glue for the plastic or HDPE/UHMWPE + PE wax for the core materials…
Third:
Now I "just" need to start modelling the skeleton and "simply" making the muscles.

This is that moment that deep down in my lizard brain that makes me think:
"This thing might kill me"
We are taking about kilovolts that could easily make my heart stop.
Although the thickness of the materials will differ, and thus, the input voltage may be lower, we are still talking about inserting 81 Kilowatts of power in the shape of high voltage low amperage.
And on top of that, it will require the same mechanical brakes as the other artificial muscles, so I'm starting to ask myself it is worth the trouble...
Shouldn't I instead work with the thermal artificial muscles...?
Well, this is me from the future, and I finally went to check the price of mechanical/electromagnetic brakes and winches with the lifting capacity closer to the intended input force (3000kg), and guess what?
It is too expensive and heavy. :|
With the exception being the manual winch brakes, which would need to be modified for higher load and also for the insertion of a encoder:
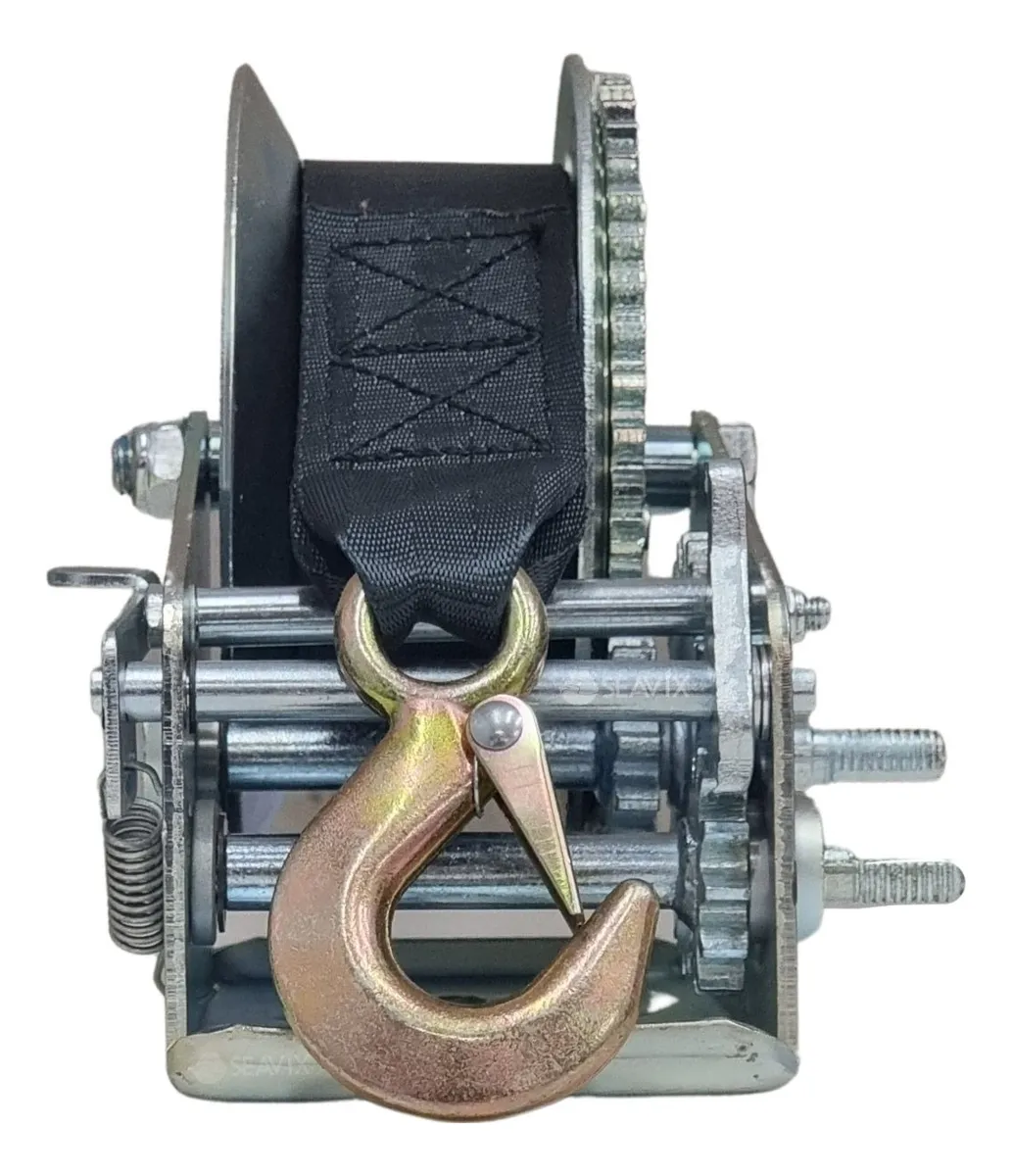
Mech design:
I want to make some of the parts of the mech biomimetic, I was thinking on making artificial cartillage (gels attached to the joints of the skeleton), artificial ligments (cables/ropes attached to the skeleton) and tendons (ropes covered in pva).
I'm just not that confident on my skills, neither in how long/strong will these parts actually hold on. I say this because some parts of the human body can reach 1 GPa of tensile strength. That is close to carbon fiber, now imagine an elefant or a horse...
You know what? I will "study" (look at videos) the anatomy of elefants, horses, rhinos, hippos and all sort of heavy animals in order to take inspiration/copy their structure for the mech. By the way, elefants can weight from 2700kg to 6000kg depending on the race, horses can weight from 150kg to 1500kg depending on the race, hippos range from 1300kg to 1800kg and rhinos 2500kg to 3200kg. These values are the average, the elefants can even get up to 10 tons.
In both cases, what concerns me is the relaxation of the artificial tendons, ligments and muscles.
This video is about a reduction pulley that uses ropes, and after a while, the ropes start creep. The guy was forced to use Dyneema for it, which has the lowest extension in the market, but it is also very expensive. However, his actuator is a precision actuator, not a biomimetic artificial tendon made in the trash (like mine), so I don't know how much it would affect my project.
Accordingly to this document, irreverssible rope creep can happen after a few years. Well, it sounds good to me, gears and bearings have the same issue of degradation over time. https://www.samsonrope.com/docs/default-source/technical-bulletins/tb_understanding-creep_mar2012_web.pdf?sfvrsn=1e71fc4e_2
Bruh, the idea that every couple of years I will need to make a "surgery" in a mech to fix its arthritis, arthrosis, tendinopathy and strains.
-
Articles that I think are interesting for biomimetic human robot:
- "Bone has yield strength of 51–66 MPa in tension and 106–131 MPa in compression when tested along its transverse axis. The Young's modulus of cortical bone is 17–20 GPa along the longitudinal axis and 6–13 GPa along the transverse axis (Toma et al., 1997)." https://www.researchgate.net/publication/336821961_Rapid_prototyping_technology_for_bone_regeneration
- "Tensile strength of the extensor tendons averaged 13,392 psi (88 MPa) while that of the flexor tendons was less, with an average of 10,944 psi. These results indicate that, of the tendons tested, the extensors are about 20 per cent stronger than the flexors." https://www.sciencedirect.com/science/article/abs/pii/0021929068900389
- "The tensile strength of cartilage from the deep zone did not show an increase in the early years but decreased continuously with age. The tensile stiffness of the superficial layer at stresses of 5 MN/m2 (5 MPa) and 10 MN/m2 (10 MPa) increased to maximum values in the third decade and thereafter decreased with increasing age." https://www.ncbi.nlm.nih.gov/pmc/articles/PMC1001032/
- " Ultimate tensile strengths for tendons and ligaments range from 50 to 150 MPa (for comparison, recall that the tensile strength of bone is about 150 MPa)." https://musculoskeletalkey.com/mechanical-properties-of-ligament-and-tendon/
- "The 'overall' strain in the ligament was calculated from the outermost pairs of markers along the ligament length. The average tensile strength, the 'overall' tensile modulus and the 'overall' strain of the ALL at failure were 27.4 MPa (S.D. 5.9), 759 MPa (S.D. 336) and 4.95% (S.D. 1.51)" https://pubmed.ncbi.nlm.nih.gov/1400518/
- https://asmedigitalcollection.asme.org/mechanismsrobotics/article/15/1/014503/1140488/Experimental-Verification-of-Kinematics-and
- https://onlinelibrary.wiley.com/doi/full/10.1002/aisy.202200126
- https://www.mdpi.com/2313-7673/9/3/151
- https://www.semanticscholar.org/paper/Design-of-a-highly-biomimetic-anthropomorphic-hand-Xu-Todorov/a4a9eff18b74cd9c2518c9f3ef164b4aab3ac276
- https://www.researchgate.net/publication/343115388_3D_Printing_an_Assembled_Biomimetic_Robotic_Finger
- https://www.researchgate.net/publication/261479910_Design_of_an_anthropomorphic_robotic_finger_system_with_biomimetic_artificial_joints
- https://arxiv.org/html/2404.06740v1/
- https://arxiv.org/pdf/2310.18283
- https://www.semanticscholar.org/paper/Design-concept-of-detail-musculoskeletal-humanoid-a-Nakanishi-Asano/91e00abaee60fd39bf9317f94338864fc9701666
- https://www.semanticscholar.org/paper/Human-mimetic-musculoskeletal-humanoid-Kengoro-real-Asano-Kozuki/afba83157286c9892a8715511b6b9d0ce99ac506
- https://www.mdpi.com/2072-666X/12/9/1124
- https://arxiv.org/pdf/2012.10981
- https://salford-repository.worktribe.com/preview/1503213/T_RO_2%20%28003%29.pdf
- https://www.semanticscholar.org/paper/Fluid-Lubricated-Dexterous-Finger-Mechanism-for-Kim-Yoon/94cb1c73b7eff9ed8af0bf07e95f1d3297774169
- https://www.semanticscholar.org/paper/On-the-Optimal-Design-of-Underactuated-Fingers-Boisclair-Lalibert%C3%A9/0d132d7f3dff8da409ca2bb096f973ed5cb3ac38
- https://engineering.stackexchange.com/questions/19547/what-is-this-kind-of-bearing-called
- https://www.researchgate.net/publication/346997961_A_flexible_self-recovery_finger_joint_for_a_tendon-driven_robot_hand
- https://josr-online.biomedcentral.com/articles/10.1186/s13018-019-1234-6
- https://www.semanticscholar.org/paper/The-DLR-hand-arm-system-Grebenstein-Albu-Sch%C3%A4ffer/571c8c6aa4a0da330c7266ba2f0d951d1775922b
- https://elib.dlr.de/93329/1/Wolf2014_VIA_PPRIME.pdf
- https://www.sciencedirect.com/science/article/abs/pii/S0029801822011465
- https://www.semanticscholar.org/paper/Biomimetic-design-of-musculoskeletal-humanoid-knee-Asano-Mizoguchi/bc767a23d95de2cce4514020533bbf23eaf590e2
- https://www.sciencedirect.com/science/article/pii/S1751616123001613
- https://www.mdpi.com/2313-7673/9/3/164
- https://www.researchgate.net/publication/304190275_An_Overview_of_the_Ongoing_Humanoid_Robot_Project_LARMbot?_tp=eyJjb250ZXh0Ijp7ImZpcnN0UGFnZSI6Il9kaXJlY3QiLCJwYWdlIjoiX2RpcmVjdCJ9fQ
- https://www.researchgate.net/publication/304190275_An_Overview_of_the_Ongoing_Humanoid_Robot_Project_LARMbot
- https://www.researchgate.net/publication/286342185_Actuation_Principles_for_the_Bioinspired_Soft_Robotic_Manipulator_SpineMan
- https://www.cureus.com/articles/9512-the-barrow-biomimetic-spine-comparative-testing-of-a-3d-printed-l4-l5-schwab-grade-2-osteotomy-model-to-a-cadaveric-model#!/
- https://josr-online.biomedcentral.com/articles/10.1186/s13018-022-03012-9
- https://www.semanticscholar.org/paper/Biomechanical-study-of-lumbar-spine-with-artificial-Han-Lee/4790928247fd6b5604e475a8d1133c6a171f4525
- https://www.researchgate.net/publication/228086806_Finite_element_analysis_of_artificial_disc_with_an_elastomeric_core_in_the_lumbar_spine
- https://www.researchgate.net/publication/258359443
- https://tensegritywiki.com/index.php?title=Spine
- http://www.biotensegrity.com/resources/tensegrity-truss-spine.pdf
- https://www.researchgate.net/publication/322280616_Design_and_kinematics_analysis_of_a_novel_six-degree-of-freedom_serial_humanoid_torso
- https://www.researchgate.net/publication/253241653_Dual_Arm_and_Multi-segment_Spine_Motion_Control_for_Assistive_Humanoid_Robots
- https://www.researchgate.net/publication/221710009_A_Musculoskeletal_Flexible-Spine_Humanoid_Kotaro_Aiming_at_the_Future_in_15_Years_Time
- https://www.researchgate.net/publication/272922007_Design_Approach_of_Biologically-Inspired_Musculoskeletal_Humanoids
- https://www.sciencedirect.com/science/article/pii/S2405844023007478
- https://www.researchgate.net/figure/The-LAB-human-and-dummy-models-BAUDRIT-HAMON-SONG-ROBIN-and-LE-COZ-1999-LIZEE_fig10_292731361
- https://www.lsoptsupport.com/documents/papers/robustness/2010-earlier/test-paper
- https://www.semanticscholar.org/paper/Analysis-of-using-an-active-artificial-spine-in-a-Kuehn-Dettmann/661cd2797d9582ebf68f2a248f3288df621d52e7
- https://www.semanticscholar.org/paper/Design-of-upper-limb-by-adhesion-of-muscles-and-%E2%80%94-Kozuki-Motegi/63b81a6cd95cba47851ed7bcf5b4dfdc2c02ade2
- https://www.semanticscholar.org/paper/Design-of-a-biologically-inspired-humanoid-neck-Barker-Fuente/512e22a3efdd64558daf12c083c8fe21368b6383
- https://homes.cs.washington.edu/~todorov/papers/XuICRA16.pdf
- https://tbirehabilitation.wordpress.com/2018/08/23/review-moving-toward-soft-robotics-a-decade-review-of-the-design-of-hand-exoskeletons-full-text-html/
- https://www.semanticscholar.org/paper/Design-of-a-3D-printed-hand-prosthesis-featuring-Cuellar-Plettenburg/8a34cdad7d408beaaa27ad2969b8fb346f9be629/figure/4
- https://www.researchgate.net/figure/5-The-skeleton-of-the-3D-printed-finger-connected-by-crocheted-ligaments-and-laser-cut_fig3_338912205
- https://www.researchgate.net/figure/A-the-CAD-assembly-of-the-proposed-biomimetic-human-index-finger-design-B-the-design_fig2_343115388
- https://www.science.org/doi/pdf/10.1126/scirobotics.aaq0899
- https://www.ncbi.nlm.nih.gov/pmc/articles/PMC1571305/
- https://pubs.rsc.org/en/content/articlelanding/2021/bm/d0bm01852j
- http://davidbuckley.net/RS/HandResearch.htm
- https://www.semanticscholar.org/paper/On-the-Optimal-Design-of-Underactuated-Fingers-Boisclair-Lalibert%C3%A9/0d132d7f3dff8da409ca2bb096f973ed5cb3ac38
- https://www.frontiersin.org/articles/10.3389/frobt.2023.1164660/full
- https://www.researchgate.net/figure/Biaxial-Compliant-Rolling-contact-Element_fig2_267837075
- https://h2t.iar.kit.edu/pdf/Beil2018a.pdf
- https://www.researchgate.net/publication/365216860_Bio-inspired_design_of_a_self-aligning_lightweight_and_highly-compliant_cable-driven_knee_exoskeleton
- https://www.researchgate.net/figure/Proposed-1-DoF-joint-mechanism-using-the-rolling-joint_fig4_370924703
- https://www.researchgate.net/figure/Rolling-contact-articulations-can-be-employed-instead-of-standard-revolute-joints-to_fig4_326398115
- https://ras.papercept.net/images/temp/IROS/files/2632.pdf
- https://www.cs.cmu.edu/~cga/c/0749.pdf
- https://www.researchgate.net/publication/282389660_Design_Considerations_for_a_Hyper-Redundant_Pulleyless_Rolling_Joint_With_Elastic_Fixtures
- https://srl-ethz.github.io/get-ball-rolling/
- High tensile poly(vinyl alcohol)/Carboxymethyl cellulose sodium/Polyacrylamide/Borax dual network hydrogel for lifting heavy weight and multi-functional sensors | Cellulose (springer.com) (Mixing borax with polyvinyl alcohol turns it into a really good viscoelastic material that could be used as the biomimetic artificial cartillage for the mech, I do enjoy how PVA can be so versatille)
- https://link.springer.com/article/10.1007/s10853-023-09061-7
A rubber pad for hydraulic jack with a diameter of 115mm and thickness of 35mm can withstand 2500kg, and accordingly to compressive strength calculator, the force in MPa would be around 2.3 MPa. So a compressive strength of 8 MPa would be 3.47 times that value (assuming the same diameter of 11.5cm), so: 8695.6kg. Obviously, I do intend on using other materials for the composite and increasing its strength, like starch, cellulose fibers, borax and even sodium hydroxide with fumed/fused silica powder. The addition of 1:1:0.1 of PVA, starch and cellulose alone can double or even triple its tensile strength.
I said "biomimetic", but boy, do I say BOY, the idea of simply going full anatomical copy of the human body is extremely tempting.
The reason why this is a bad idea:
- Human body has 206 bones
- More than 650 skeletal muscles (muscles attached to the skeleton)
- 900 ligaments
- 4,000 tendons.
So, I was wondering which should be the height of the mech. Well, I actually found proportional human height calculator:
https://hpc.anatomy4sculptors.com/

And as such, you could insert the height of a person in a determined position in order to check how tall the mech should be in order to fit the pilot inside of it.
For example, if the pilot has 185 cm of height (1.85 meters), its thigh/femur would have around 46cm long, and if you assume this person is in a sitting position, then you just need to reduce the length of the thigh by the total length 185-46 = 139cm. If you insert this length in one of the parts, the other measurements will be in proportion to that. For example, if you add this length of 139cm to the square where it says "from shoulder line to navel", the total height including head would be around 6,6 meters tall (5.7 meters without the head).
By the way, if you assume the leg of the Mech in the art of this project has around 1,9 meters of height, the total height of the mech would be around 7,5 meters tall.
Well, I settled for the height of this 185cm tall person in a crouch position to be a little more than 90cm, so the entire height including the head of this mech would be around 3,8 meters tall (without the head).
Of course, you could change this whatever way you want to, but it would stil give an idea on how big the mech should be in order to fit the pilot and on top of that, all of the equipment. And I do think this is too tall since the floor to the ceiling of my room is just 2,5-2,6 meters tall, and I don't see the reason for a mech that needs to be crouched to fit in a room.
By the way, using the square cube law and assuming that a 1,80 meter tall human weights around 80kg to 100kg, a 3,6-3,8 meter tall human would weight around 640kg to 800kg.

So you can have an idea on how much weight this mech would weight in this scenario.
Obviously, I don't know yet what are the exact dimensions of the pseudo-bones/endoskeleton of the mech, since they are meant to be biomimetic and not a 1:1 scale.
Besides, the human skeleton is capable of enduring 30 times its own weight, so i would need to make it around 10 times thicker/stronger in order to survive the thousands of kilograms I intend on making it lift.
It just occurred to me that I could just make cylinders actuated by the HASEL/DEA actuators instead of a biomimetic mess that would be harder to build and maintain…

That is a way of doing that alright. Obviously I’m not gonna do this way, but you get the ide
-
Also, links relevant for heavy animal anatomy:
- https://www.turbosquid.com/pt_br/3d-models/asian-elephant-anatomy-3d-model-1387620
- https://wellcomecollection.org/works/g9646xnk
- https://archaeonewsnet.com/elephants-sixth-toe-discovered/
- https://globalelephants.org/rambas-feet/
- https://www.reed.edu/biology/courses/BIO342/2011_syllabus/2011_websites/Stu_Sara/mechanism.html
- https://www.researchgate.net/publication/360938306_AN_INVESTIGATION_INTO_MANAGEMENT_METHODS_TO_PROMOTE_FOOT_HEALTH_AND_LOCOMOTION_IN_CAPTIVE_ASIAN_ELEPHANTS_ELEPHAS_MAXIMUS
- https://pressbooks.umn.edu/largeanimalanatomy/chapter/distal-limb/
- https://pressbooks.umn.edu/largeanimalanatomy/chapter/thoracic-limb-forelimb/
- https://www.researchgate.net/publication/8371421_Musculature_of_the_crus_and_pes_of_the_African_elephant_Loxodonta_africana_Insight_into_semiplantigrade_limb_architecture
- https://animaltherapeutics.com.au/stifle-injury-in-horses/
- https://www.semanticscholar.org/paper/Osteology-of-the-pelvic-limb-of-the-African-Smuts-Bezuidenhout/08100c84e73bc4d8a7de5501ec98132c36310e2d
Off-topic:
While I was reading manga, it got me wondering:
Wouldn't it be cool if there was a mathematical system and/or a programming system based on magical circles and the like?

I'd say that they would need to be intuitive, dynamic and work with the already stablished system in order to work properly...
You may think it too much of a difficult task, but just look how Japanese people makes multiplication:

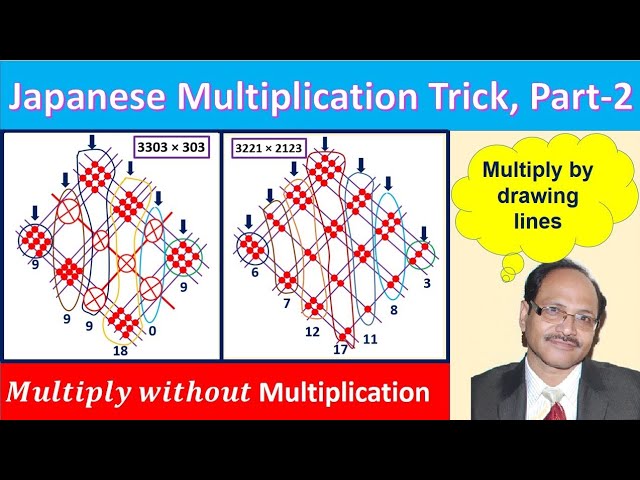
Don't tell me this doesn't look like a magic circle, lol.
Also, while image searching, I just found out that there is a mathematical "magic circle" made by a chinese named Yang Hui.
I do wonder what else strange mathematical systems one could find while digging around history... huh
Discussions
Become a Hackaday.io Member
Create an account to leave a comment. Already have an account? Log In.
I've also been waiting all day for Hackaday.io to get back online these past 2 days. I went to Hackaday.com and there was nothing under the "NOW ON HACKADAY.IO" section so I believe the site is down for everyone.
Are you sure? yes | no
dang
Are you sure? yes | no