During our initial investigations and ideations, we identified a few different somewhat-obvious pain points with respect to reducing the labor intensity of SuperAdobe, as well as a few more surprising pain points. In the end, the solutions we chose to work on addressed two specific items:
- The bottleneck of handling compass measurement for layer planning (addressed by the LIDAR Compass and Pipe Compass concepts)
- Fatigue and speed associated with bag-filling (addressed by a slightly more purpose-built earth funnel than existing ad-hoc solutions)
As conversations and development progressed, a pain point came into sharper relief that we'd previously considered, but dismissed: tamping.
Labor Intensity of Tamping/Compacting
While building a SuperAdobe structure, each layer must be compacted for shape and structural integrity. Layers must be uniformly flat on top so that loads are distributed properly through them, but they also must be compacted to a specific minimum pressure so that they don't crumble or break unexpectedly under load. Specifically, a given layer needs to be compacted such that after curing, it bears a pressure of 300psi without breaking or crumbling inside the bag.
It turns out that achieving this level of compaction isn't very difficult, and is typically done by hand with a tamping tool most often used for leveling gravel or dirt:
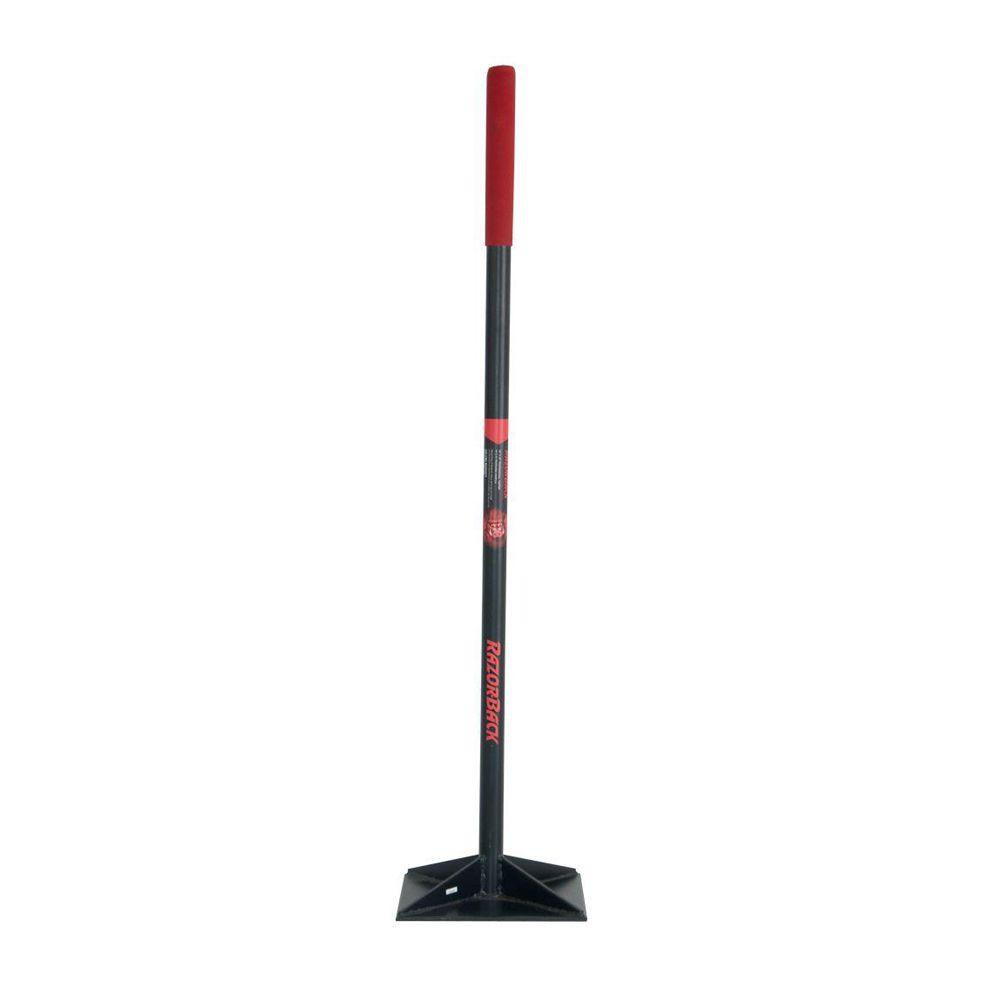
In terms of achieving the necessary results, this works just fine. The problem is, a single SuperAdobe dome has many hundreds of linear feat of bag to compact, and doing this work is tiring on top of all the other manual processes that have to take place. It also makes the build process less accessible, as tamping requires a higher level of fitness and stamina than other processes, where fitness can be traded for speed more fluidly.
Introducing Power Tools to the Mix
Luckily, laying SuperAdobe isn't the only construction task that requires tamping, and plenty of options for power tools to do this job already exist. For instance, compacting plates exist for jackhammers:
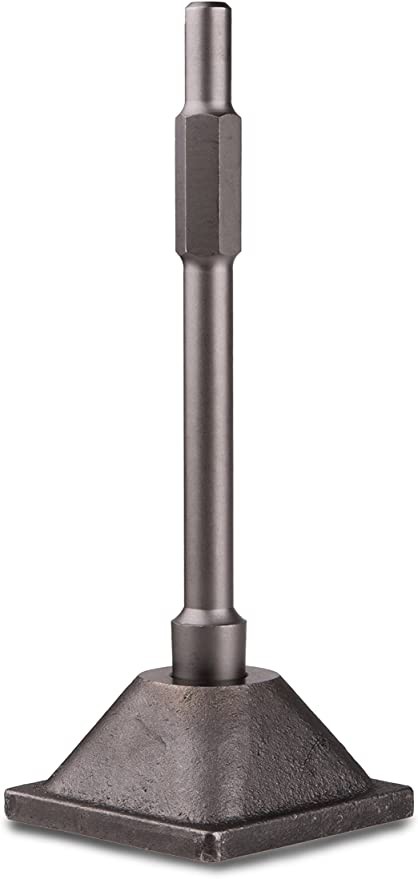
+
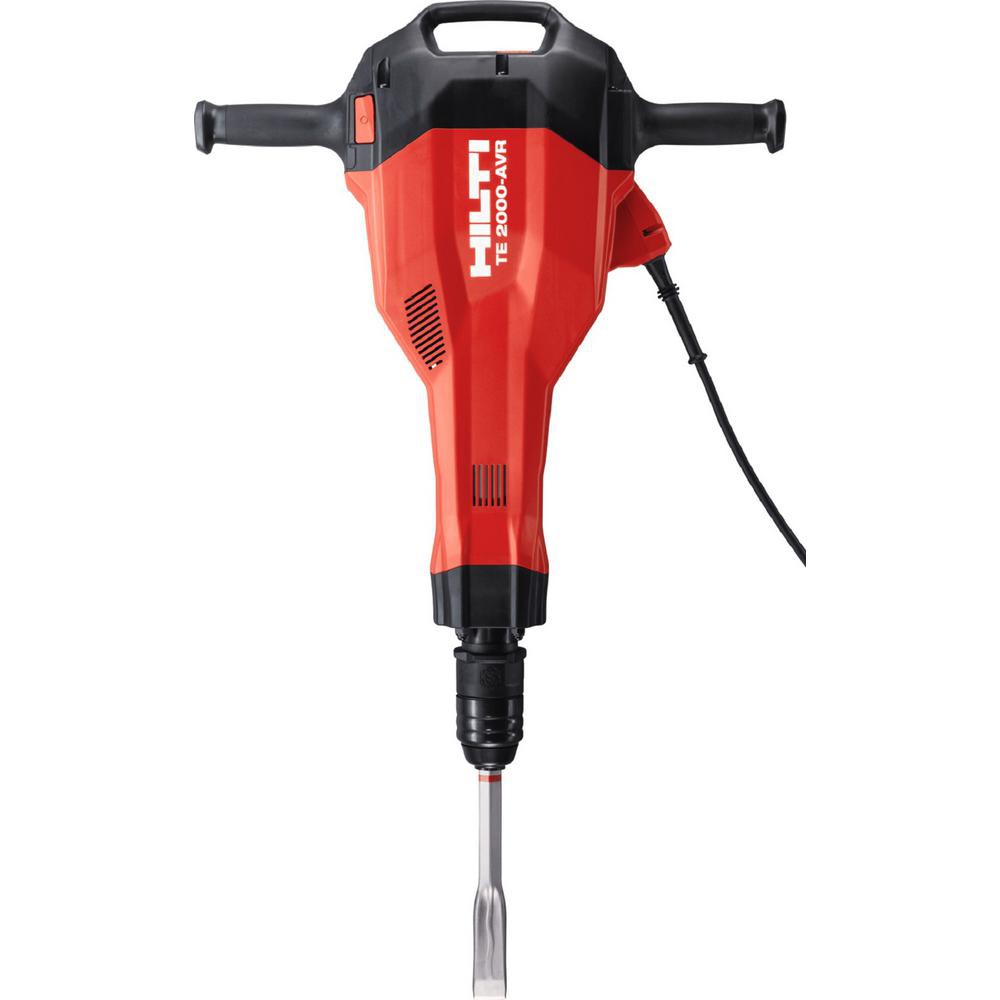
And for larger areas, an easier-to-use option is the plate compactor:
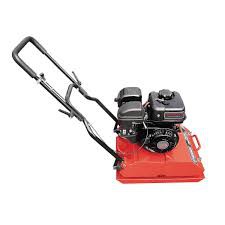
The problem is, both of these options are unwieldy and potentially dangerous perched at the top of a SuperAdobe dome, and both are terribly overkill for the compaction pressure required, to boot.
Luckily, there's one last option you can find on the shelves at Home Depot that might just do the trick: the rotary hammer.
The Rotary Hammer: Just The Ticket?
If you're like me, you probably used to walk through the tool aisle at Home Depot or Lowes, see this tool, and think "Man, how on earth is that drill so big?"
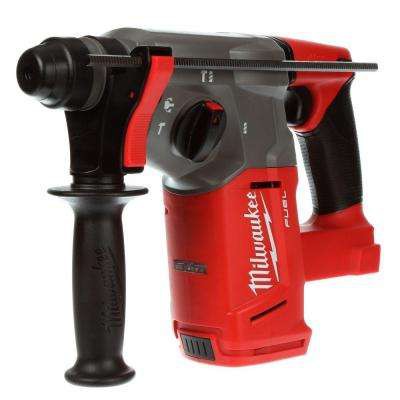
You also probably have no idea what the difference is between a "Drill," a "Drill/Driver," an "Impact Driver," and a "Hammer Drill" (And why on earth do I need an Impact Driver AND a Hammer Drill in the same kit?!). It's true, they all do EXTREMELY similar jobs, but there are subtle yet specific differences in the mechanism each uses that makes each suited to a particular job over others. In brief:
- A drill spins, usually with variable speed. It is used for drilling perpendicularly into things, with tools like twist drills, spade bits, forstner bits, and so on.
- A driver is much the same, but has an adjustable torque-limiting clutch so that you can drive screws without putting the drill itself through the same hole as you finish. You'll notice nearly every cordless drill on the market is, in fact, a drill/driver.
- An impact driver is a lot like a drill/driver, but it usually DOESN'T have a clutch mechanism, and instead has a radial hammer mechanism that serves to create a torque impulse. Imagine that you're driving a bolt with a ratchet. The bolt simply won't go any farther, so you holt the ratchet near the head and hit the handle with a hammer. An impact driver does this hundreds of times a minute. It doesn't have a torque LIMITING mechanism, but it usually has a speed control so you can throttle down on how hard the impact is, and use your trigger finger to control how many hits there are before you stop.
- A hammer drill sounds an awful lot like the impact driver, and of course also has a hammering action to it. But instead of hammering radially to make a high-torque impulse, it hammers axially to drive the drill bit into whatever you're drilling. This is specifically for masonry and concrete, where "drilling" is less about cutting and more about smashing and grinding a hole-shape into the material. The hammering action serves to chip apart the material at the end of the bit, then the flutes of the bit carry it away with rotation.
Maybe you were thinking on that last one "A power tool that hammers, huh?" - which is where my own mind went when I thought about making some kind of drill-powered tamping tool. The problem with a hammer drill is that it HAS to turn in order to hammer. We want to compact our masonry wall, not drill through each layer as we go. (Before you get clever and think about blunt drill bits against a spreader plate: you also have to have a torsional load on the bit in order to GET the hammering action - the bit needs to be going in something offering significant resistance).
Luckily there's one tool in this same family that we've left out, and you've probably guessed already what it is: the rotary hammer.
How The Rotary Hammer Works
Hammer drills are good, but like most tools, they have an upper limit on what they can handle. Hammer drills are good for screwing hose racks into a concrete foundation or maybe bolting a hand rail onto a patio slab. You need something a little beefier if you plan to attach hundreds of warehouse racks to concrete with a bunch of 1/2" wedge anchors. Where hammer drills use a relatively meek cam-slip system to hit, rotary hammers use a piston that packs a way larger punch.
If you're super observant, you might also notice that the rotary hammer above has a dial with 3 distinct settings (okay, more like 3.5). Rotary hammers can drill without doing anything else, and hammer drill as you would concrete or masonry, but they can also just hammer, without any rotation. This super useful setting basically makes the rotary hammer a light-duty jackhammer, and actually, this is probably the most common use for the tool. You can get all sorts of SDS chisels and cutters for things like breaking tilework off walls, breaking corrosion off steelwork, and even light-duty demolition of existing masonry and concrete. unleashing a jackhammer in your kitchen just to replace the floor is exactly as overkill as it sounds, but breaking off every tile by hand is just about equally underkill - the rotary hammer fits neatly in that gap.
To get your head in the right spot, here's a video of a (heavy duty, SDS-Max) rotary hammer doing what it does best:
It also happens to be the case that you can buy (or even make) tamping tools for rotary hammers.
I'm not sure what the market is: who needs to compact stuff in higher volume than a hand tamper, yet in confined enough space that a plate compactor won't do? But this is exactly what CalEarth needs, so I feel we may have a winner.
Test Plan
Rotary hammers come in a range of sizes and, commensurately, "hitting energy." I've noticed that the smallest and cheapest rotary hammers actually don't have a "hammer only" mode, which I guess gives you an idea of how hard they hit (or don't), for instance the Milwaukee M12 Fuel. On the other hand, the only rotary hammer tamping plate I found off-the-shelf has an SDS-Max shank (SDS is the shank standard used by rotary hammers, and comes in the smaller SDS+ and the heavier-duty SDS-Max). Limiting ourselves to SDS-Max substantially reduces tool selection and increases cost, but perhaps we should pay attention to what Bosch thinks is the minimum useful impact energy to make a tamping tool practical.
As such, the plan in my head for testing "rotary hammer as tamping tool" goes something like this:
- Get an SDS-Max rotary hammer and the off-the-shelf Bosch tamping tool, P/N HS1828 (plate) and HS1927 (shank). For reference, the Milwaukee unit above is specifically what I have in mind, and is representative of SDS-Max tools.
- Try this setup alongside the manual tampers on an actual build, and see whether the rotary hammer indeed works out to be faster and easier
- If the SDS-Max hammer does seem in practice to be more powerful than necessary, experiment with lighter/cheaper rotary hammers by modifying a blunt SDS+ bit to hit a wooden spreader or something like that.
- If the lighter-duty hammer seems to work, custom-fabricate SDS+ tampers by welding spreader plates onto SDS+ shanks.
I have an inkling that the monolithic rigid tamping setup might not actually be ideal here, but what might work better is an independent spreading plate with a rope handle on it that you can drag along the top of the layer, while using the tool in the other hand (or two people) to "hit" that plate.
The proper way to prototype and test that idea is in my mind, as above, to whip something up quickly on the job site of an actual build and see how it works or why it fails.
One Final Thought
At the end of the day, and after writing this up and reviewing footage of tamping and rotary hammers, it sure seems to me like a small electric plate compactor is the "correct" tool for the job. The only problem with that idea is that there's no such thing as a "small" plate compactor that I can find, and there's only one "electric" (which is, incidentally, as close to "small" as they get at 130lbs). Maybe this is exactly the right tool for the job, and is worth $2300. But I think we'll have to find out the hard way on a real build.
Discussions
Become a Hackaday.io Member
Create an account to leave a comment. Already have an account? Log In.