Iteration leads to progress and success ?
After about 4 iterations, tweaking the 3D prints, testing each component, each subassembly when adding each component, I think I have a reliable mechanism.
I still use the shield I made. Nothing wrong with that.
The software has been tweaked I changed the stepper driving to always leave one coil on, except when the hands are hanging down. Previously I pulsed the coil for 5-7 ms and then appropiate pause for speed control. Not going powerless during movement has made it a lot smoother and hopefully not missing steps.
It has worked for 3 hours in my home - but without the clockface (that is at the exhibition). This morning I got out there and put the improved clockworks in there.
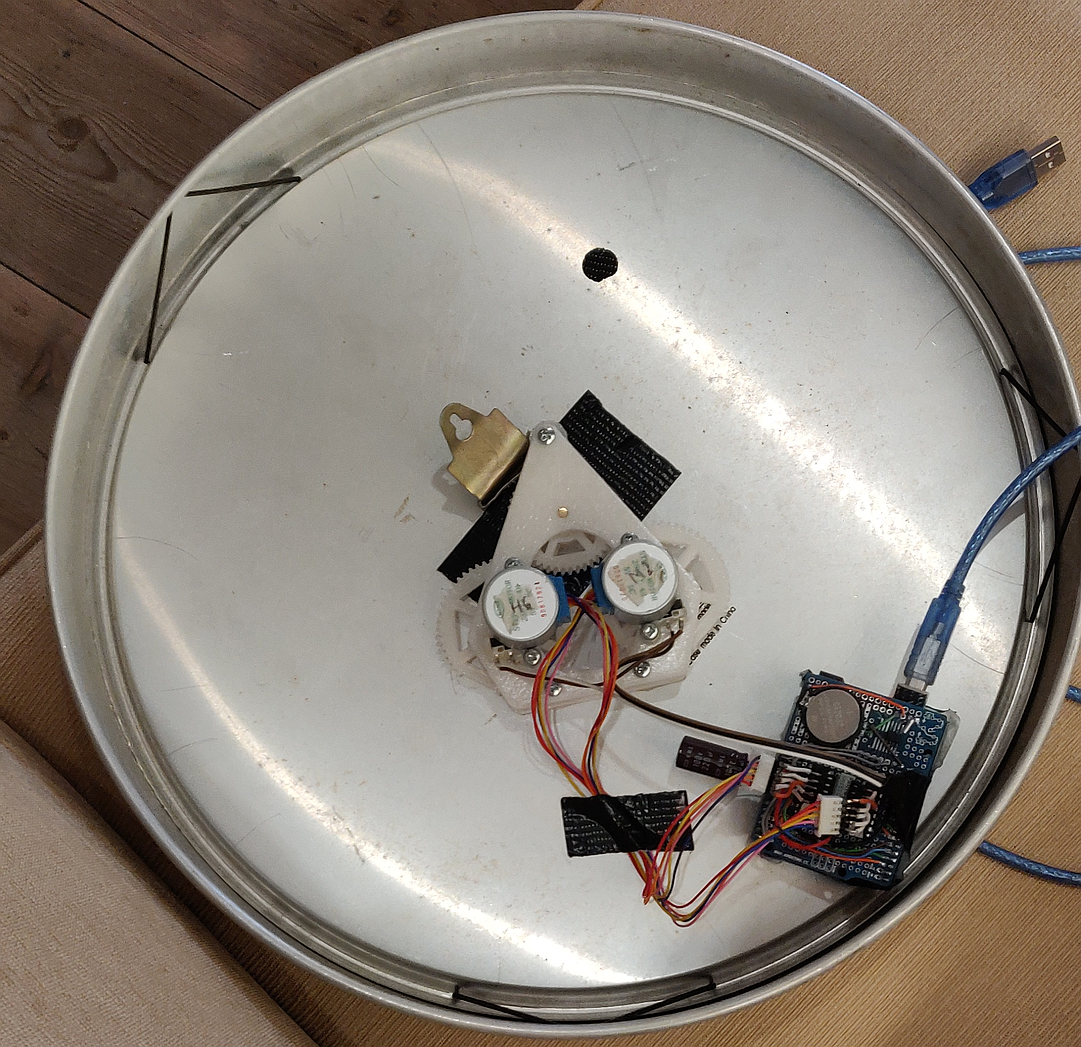
I cautiously declare it a success. [Edit after 24 hours - it still works. yeah!]
Mechanical challenges
The design is OpenSCAD (uploaded). I found out that one of the gearpairs where too close (clockmakers call this "depthing") or my homemade gearteeth where too tight (the "modulus" of a gear). This made little sense, as the OpenSCAD file specified the same distance and gear size for the other pair. Possibly there is a slight scaling error in my 3D printer, or that I slightly enlarge some holes with a drill made the distances different. To get it working I made a kludge in the OpenSCAD program to force one of the gears 1mm smaller, and tweaked toothsizes to be slimmer - and it seemed to do the trick.
I have just been nudged (by overhearing a totally unrelated conversation at a electronics store) that silcon grease is usefull for plastic gears. I'll test it at home, and if usefull apply it on the exhibition clock. It must run for 2 months, and I am not sure on wear & tear on the plastic bearings and gears.
Discussions
Become a Hackaday.io Member
Create an account to leave a comment. Already have an account? Log In.