The previous experiment left off with the assumption that a bearing of some sort would be needed on the upper end of the interior wiper. Looking back at it, it is possible that the angle formed when the interior servo arm was moving could have been caused by the cardboard. Before diving into (another) lengthy design process, verifying this happens in rigid material was needed.
The hypothesis for this experiment was that the rigid exterior magnet wiper would follow the rigid interior wiper, and the lagging angle would be minimal compared to the cardboard experiment.
At last, the result validated this hypothesis! And provides us with a usable solution to build on for the next step in the buoy release mechanism design.
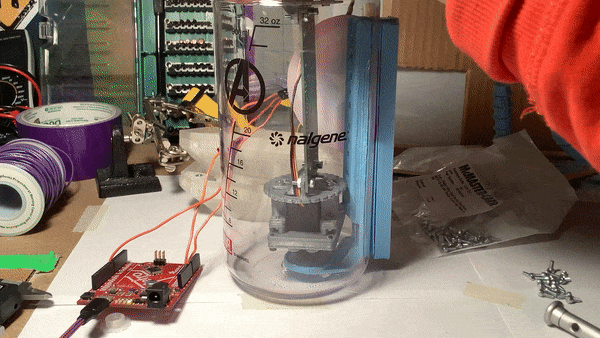
Here is the experiment setup:
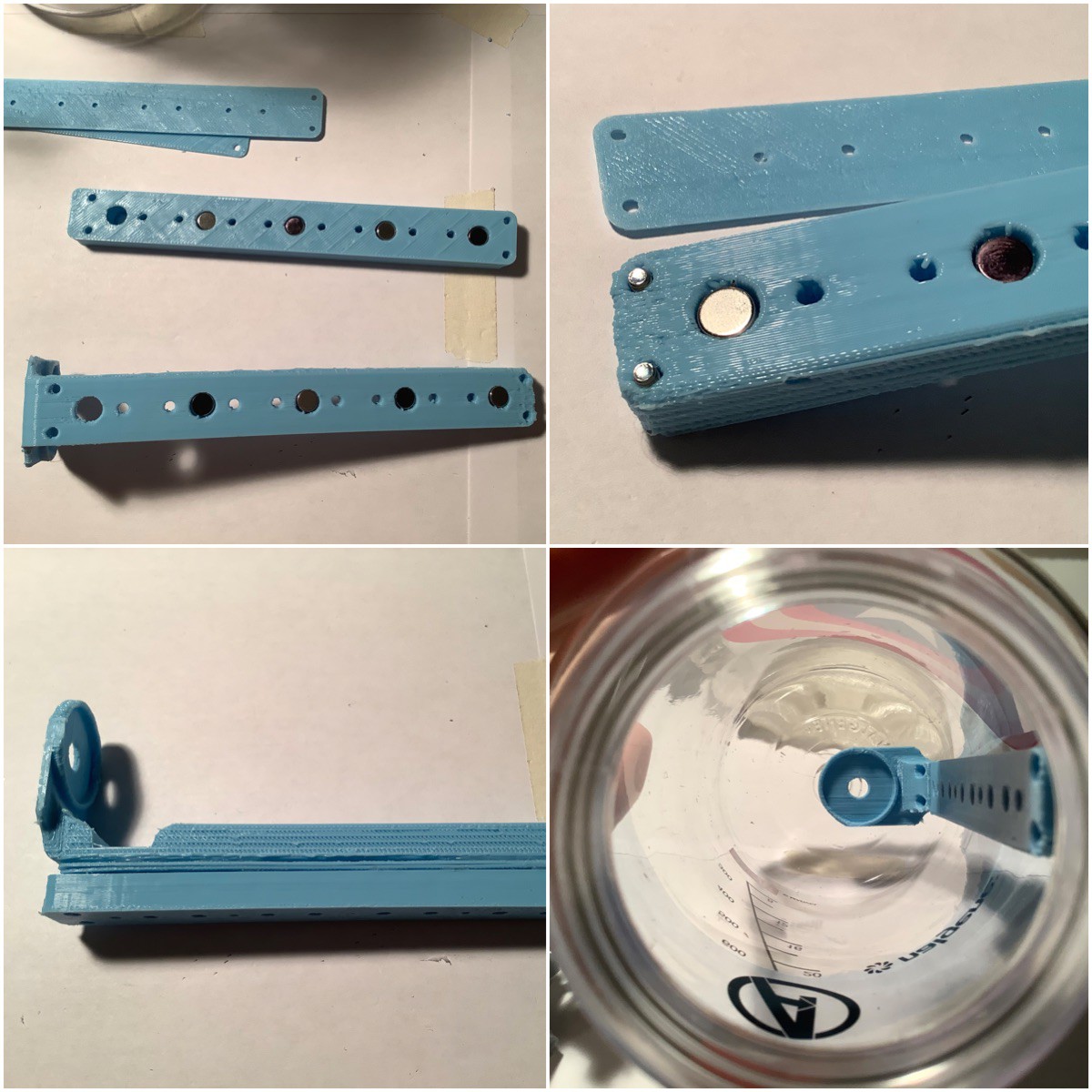
The magnets were embedded into the wiper. 4 were used for the internal, and 5 were used for external. Of interest is the bottom right image, it seems there is an offset of the servo horn. Extending this by 7mm may help reduce some of the twisting movement.
The reason why the number of magnets for the internal wiper needed to decrease (on this iteration) was because a notch for the servo bracket to pass by when the internal wiper is rotating.
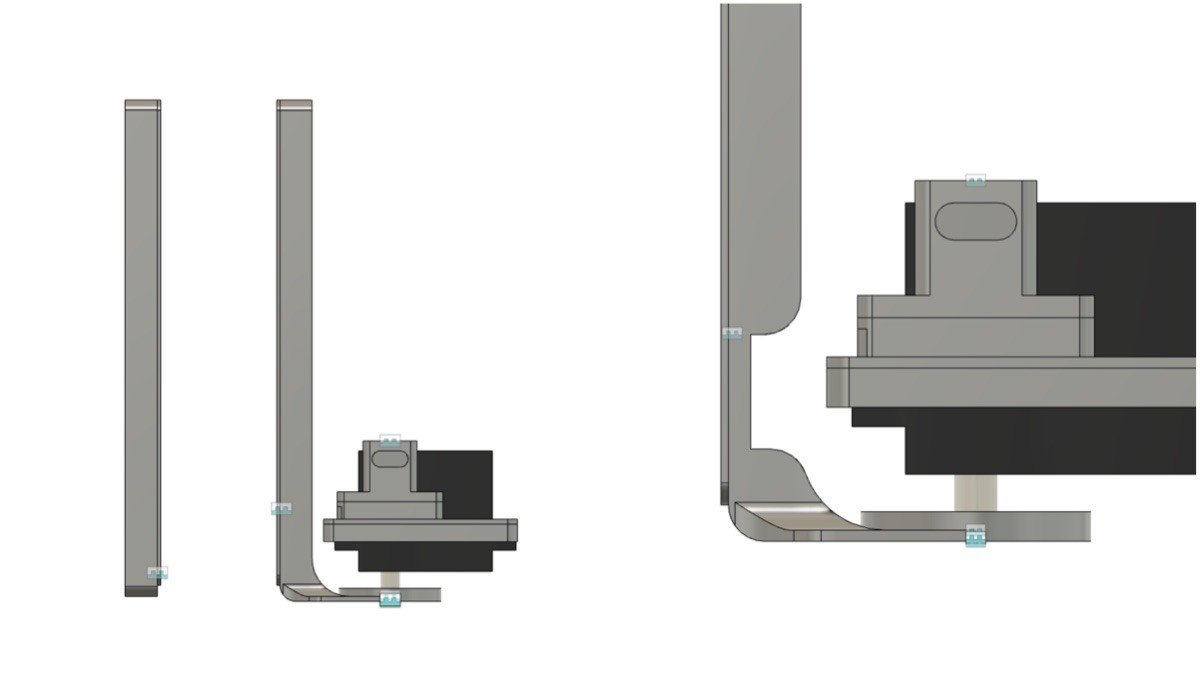
With this result, now we can iterate to build the swivelling retainer that would be situated on the top plate of the spool box where this buoy would be placed for the descent, then after some time actuate the magnetic wiper assembly to be released.
Discussions
Become a Hackaday.io Member
Create an account to leave a comment. Already have an account? Log In.