Rock intrusion continued to plague the motors, so a new traction module was designed, to fully enclose the motors.
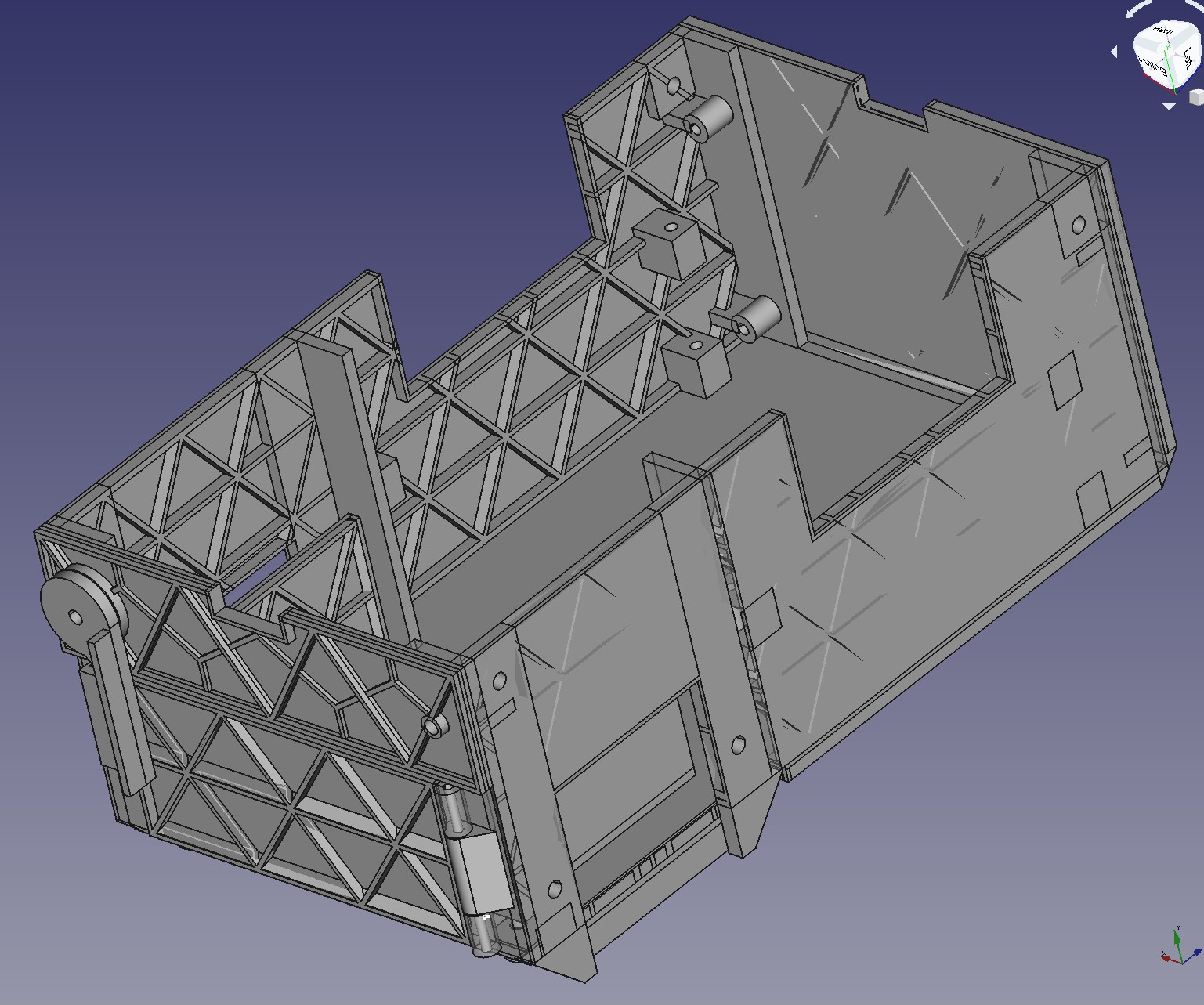
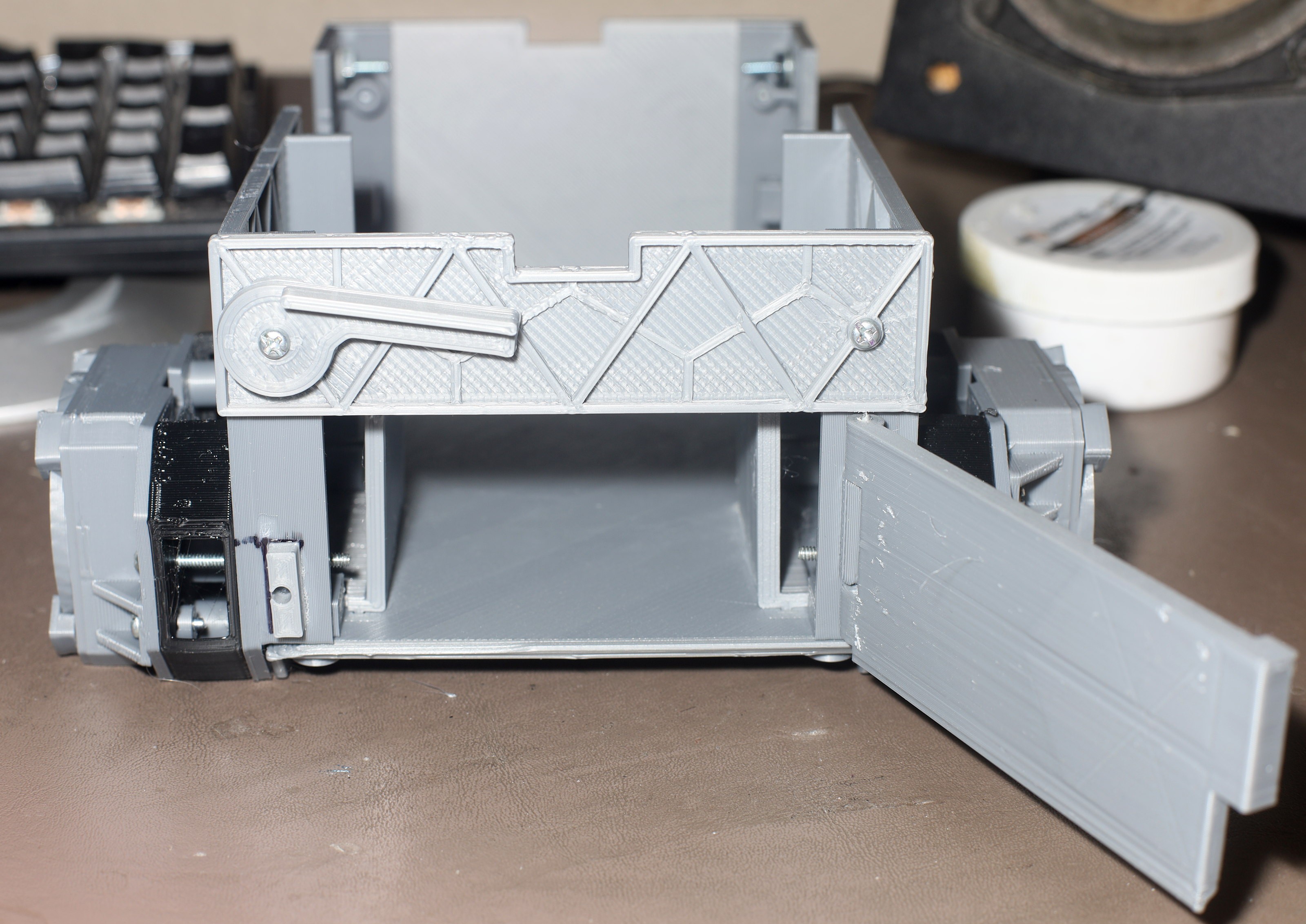
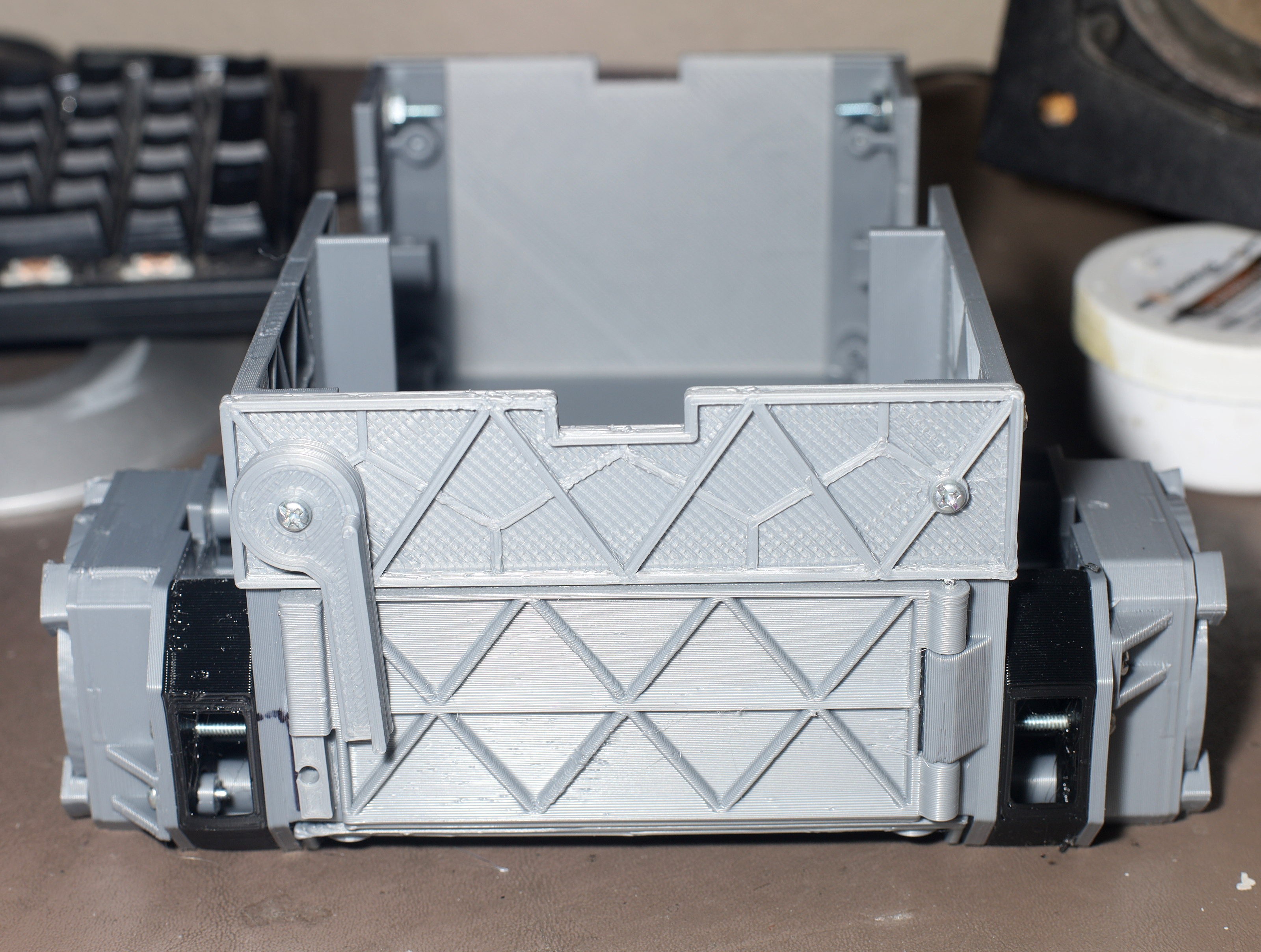
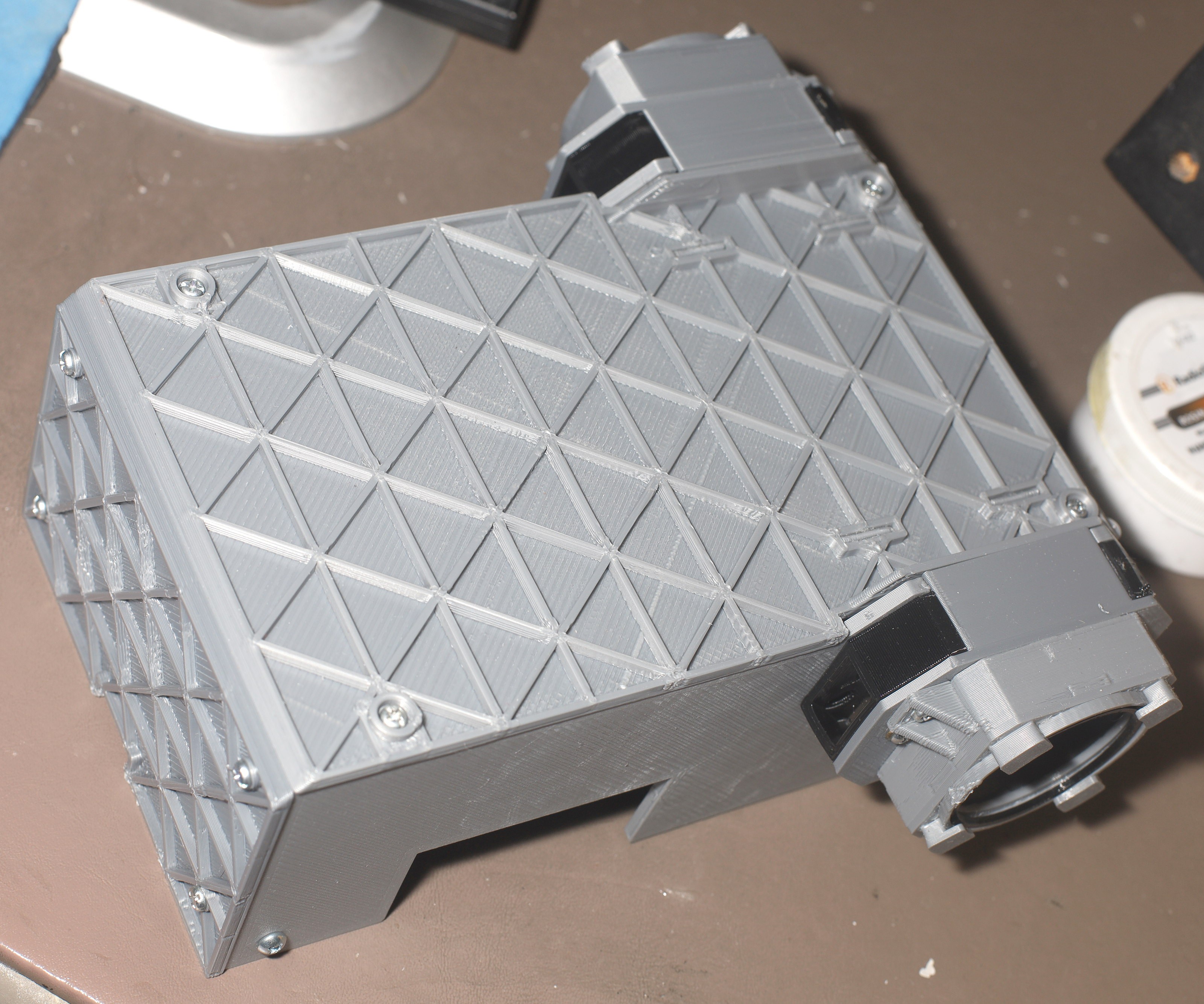
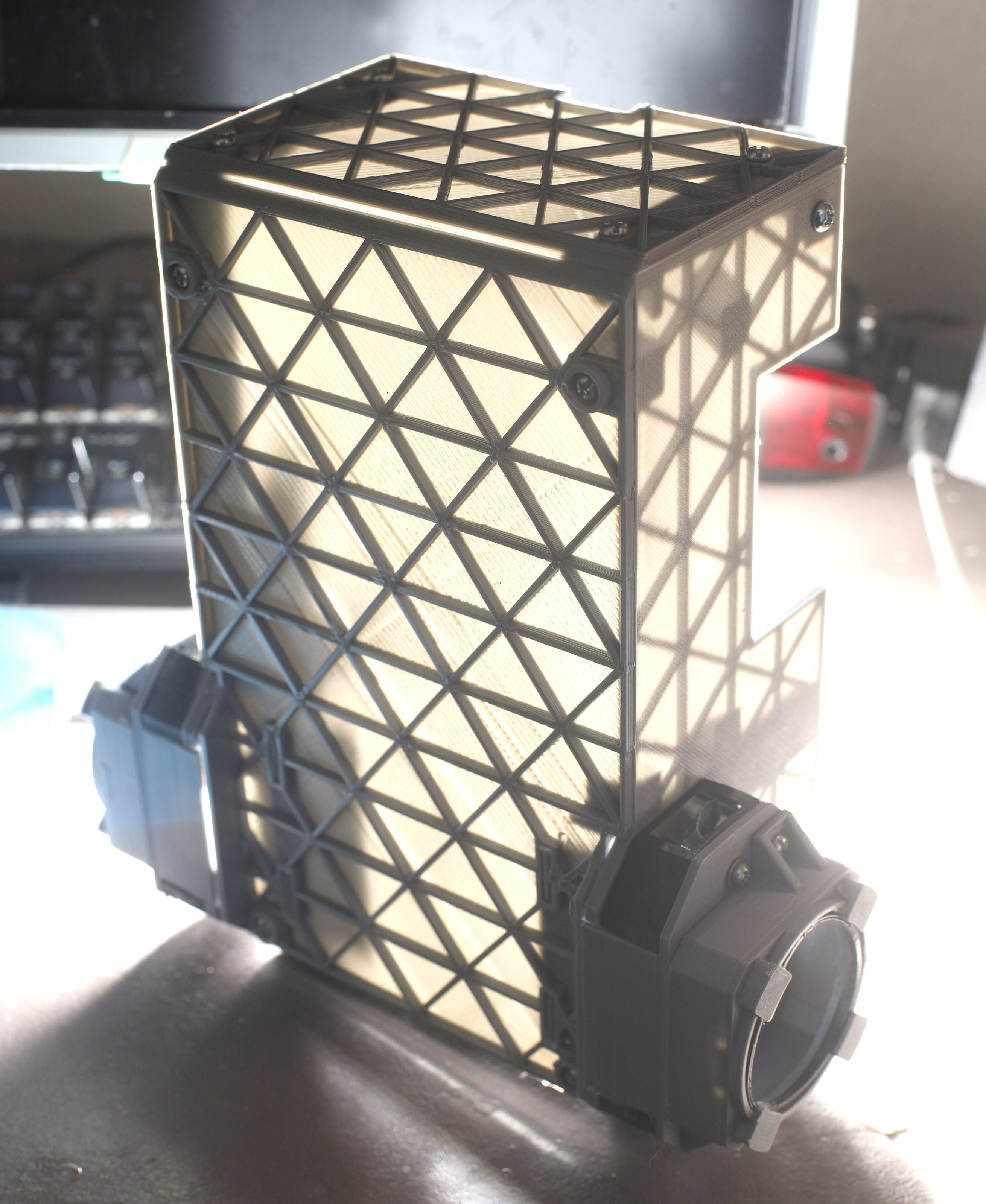
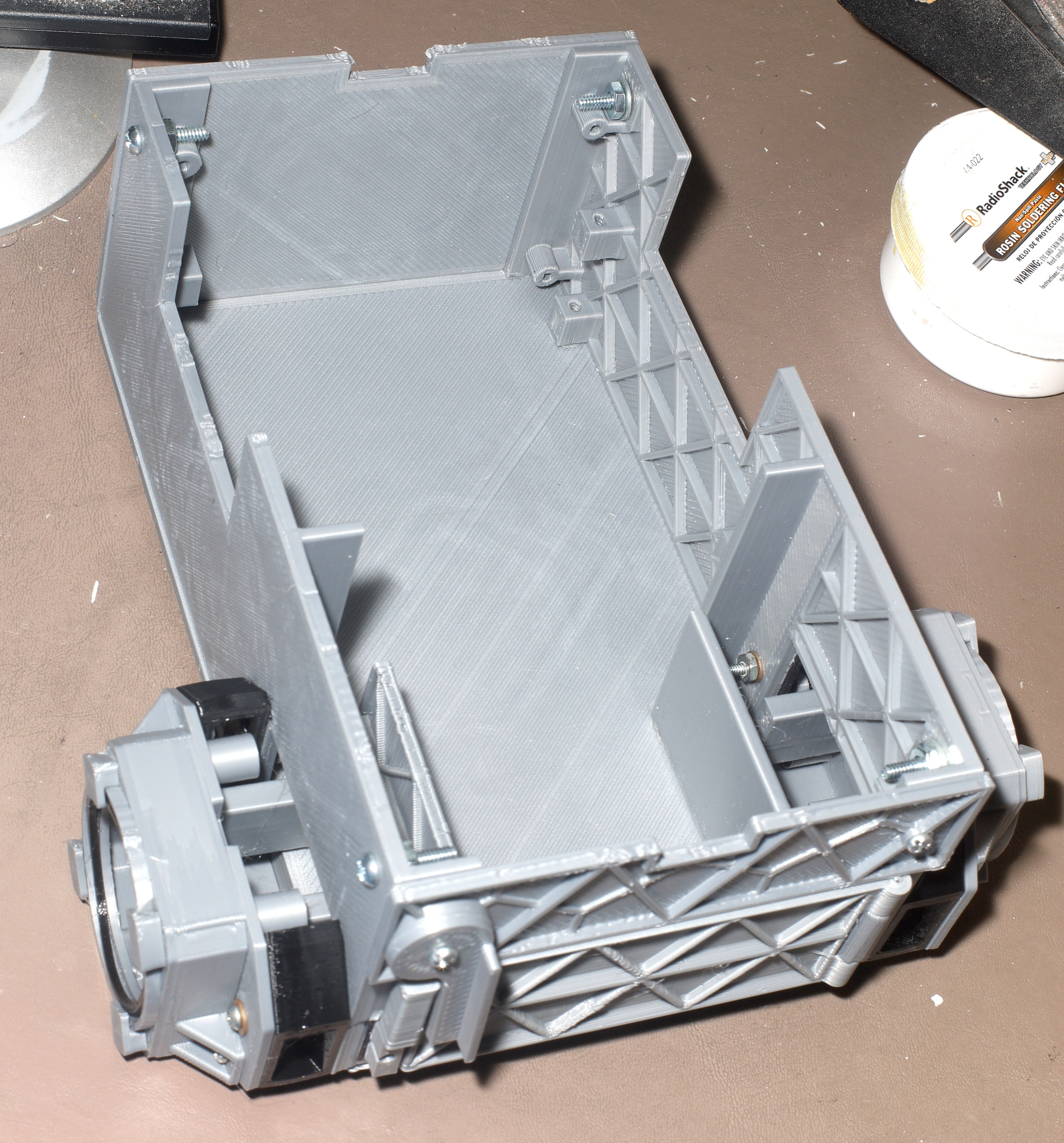
This one flipped the isogrid panels so the sides could be printed in 1 piece. It was sized for a .8mm line width, .32mm layer height. The reduced part count made it fit much more accurately.
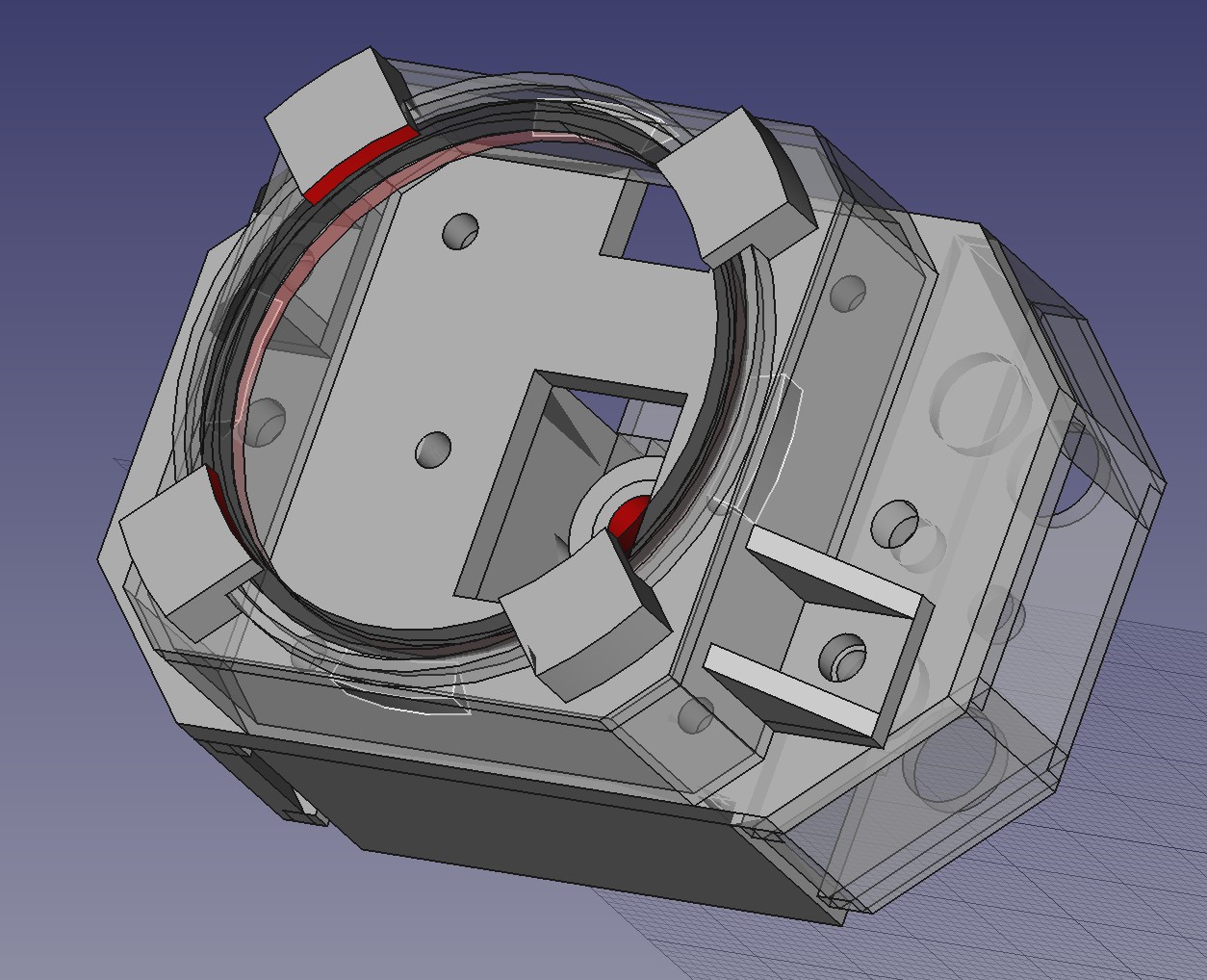
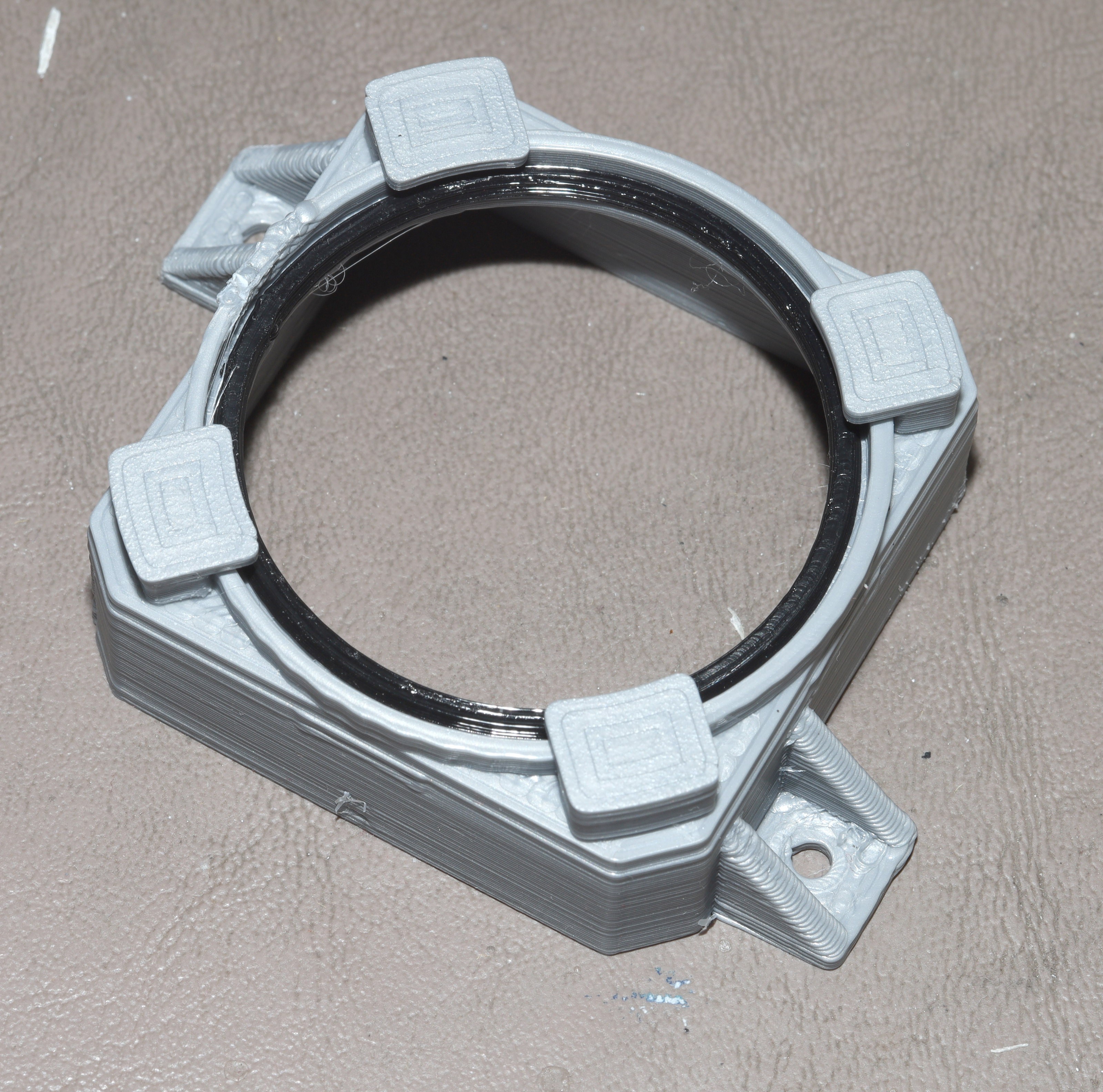
The key was a novel motor shroud with a TPU o-ring that would theoretically keep rocks out.
The encoders continued to plague the motors.
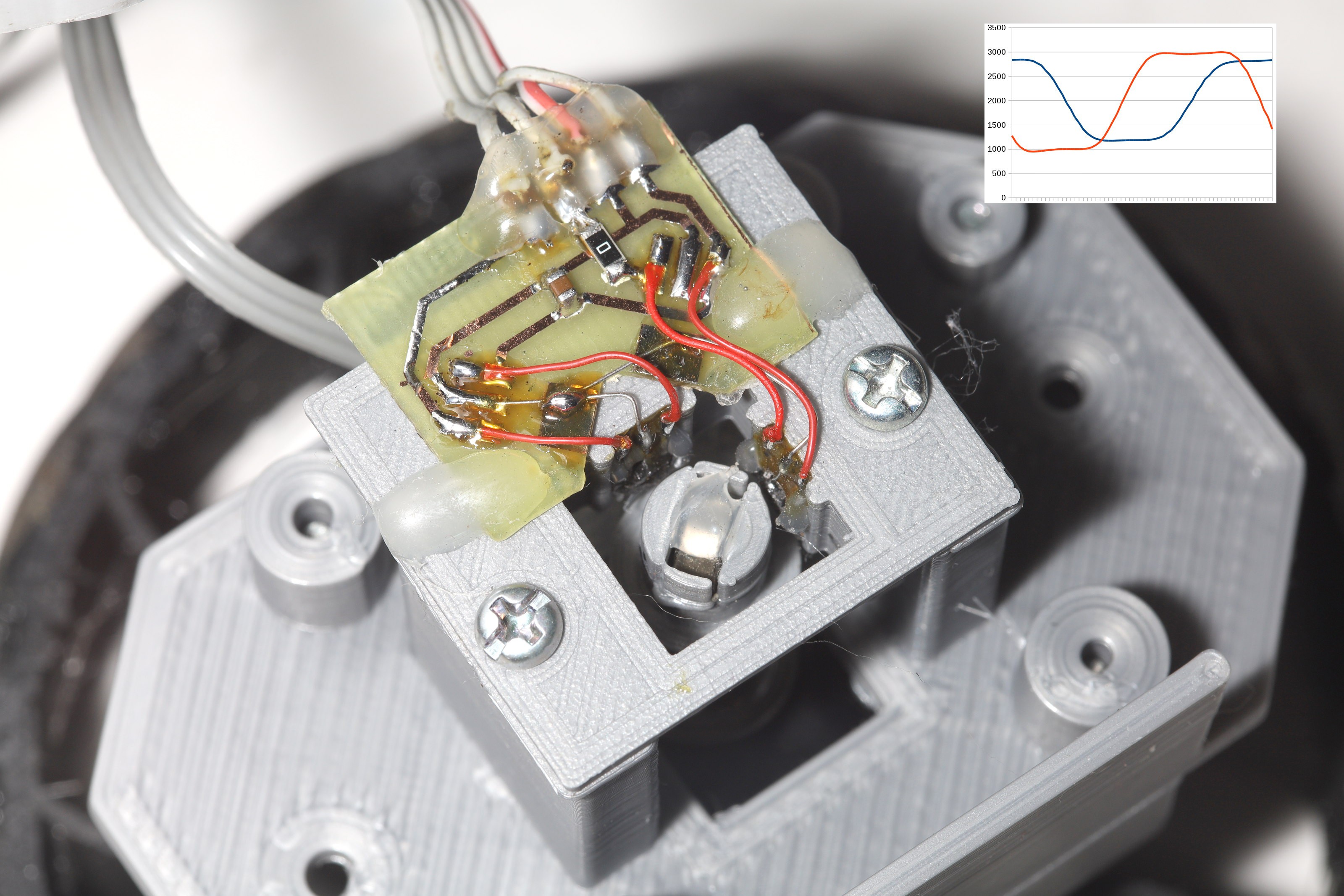
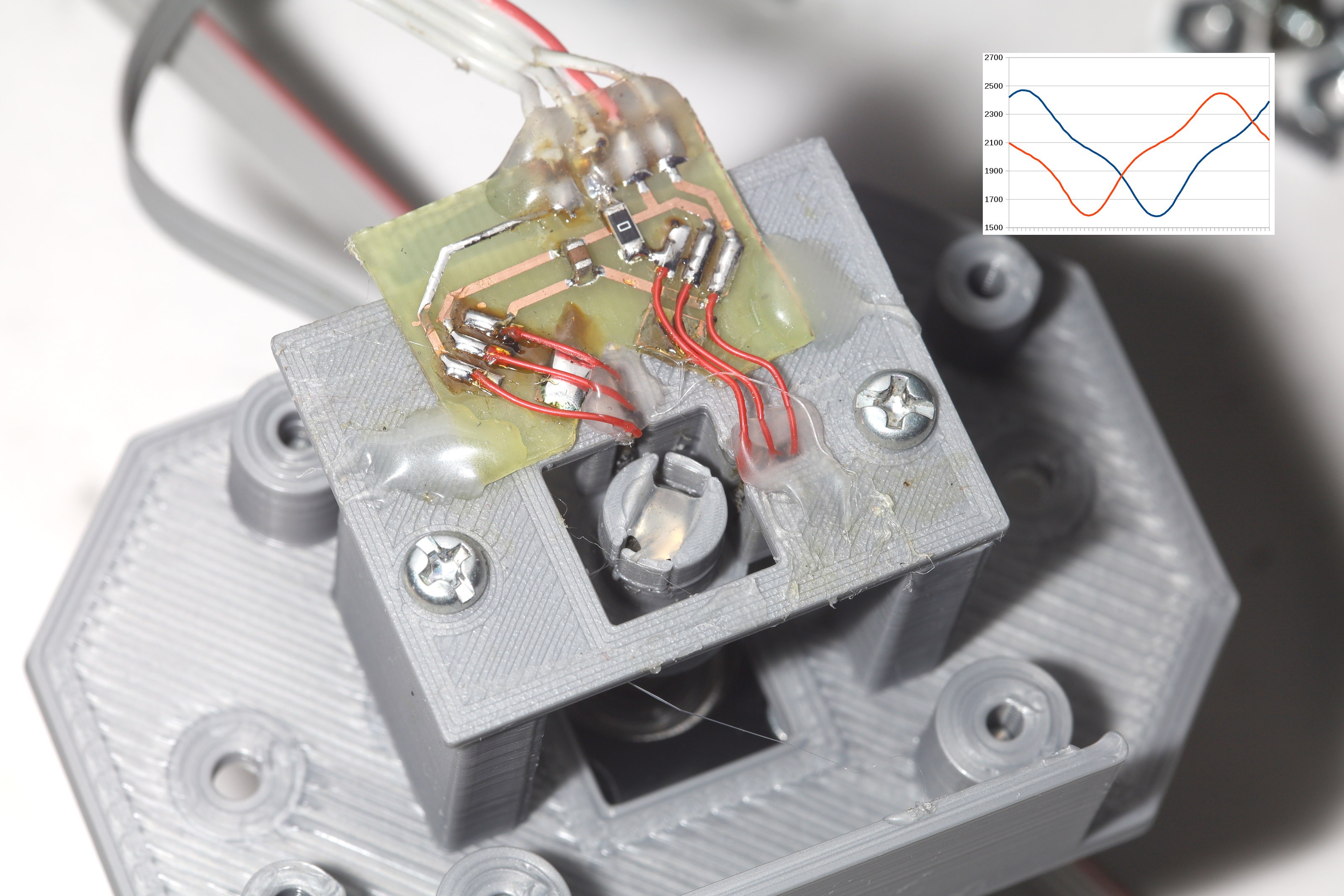
The hall effect sensors were reoriented, which allowed them to finally sense the full range of motion. They have to point along the circumference rather than radially. The resolver in this configuration is thus the easiest way to detect motor position.
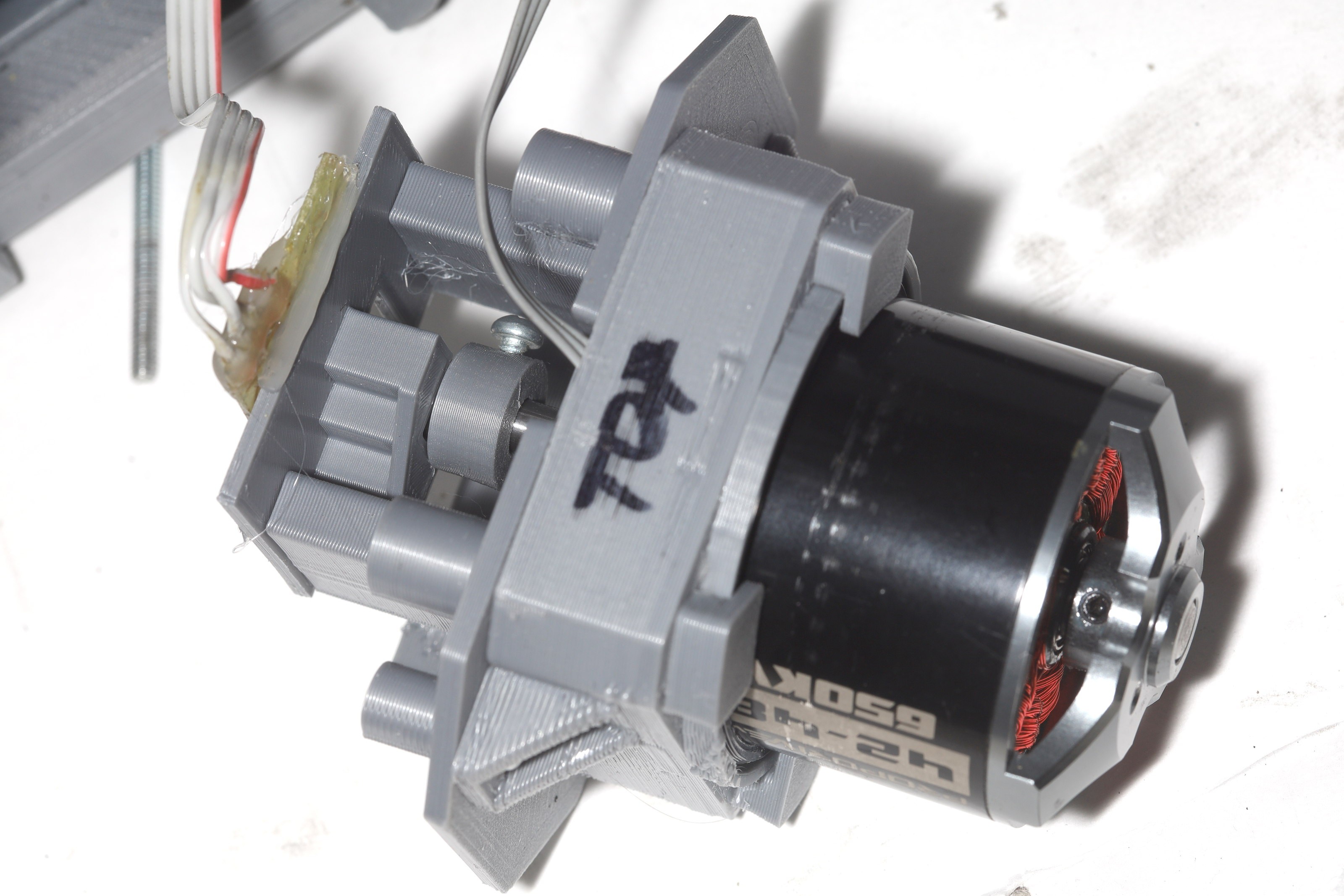
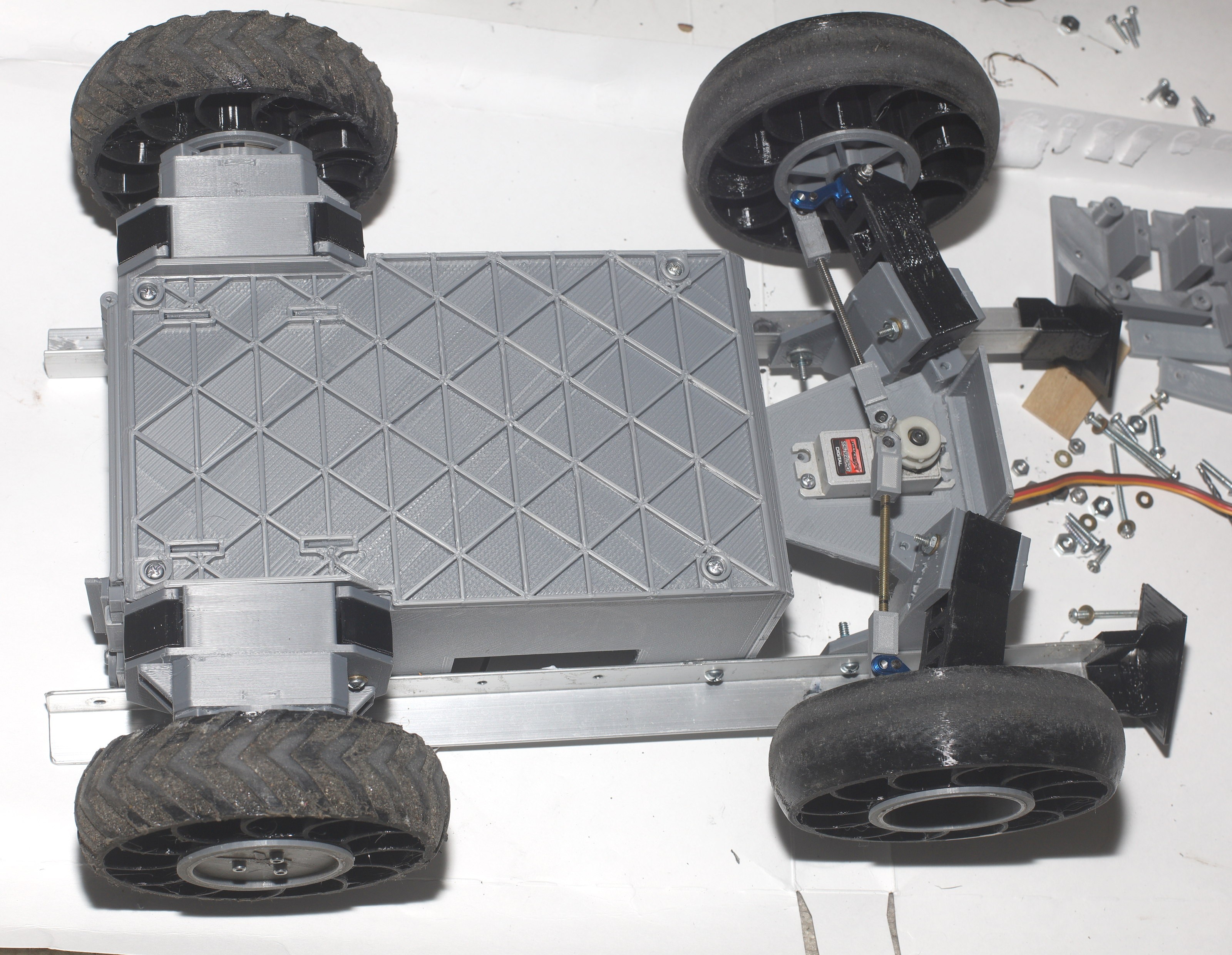
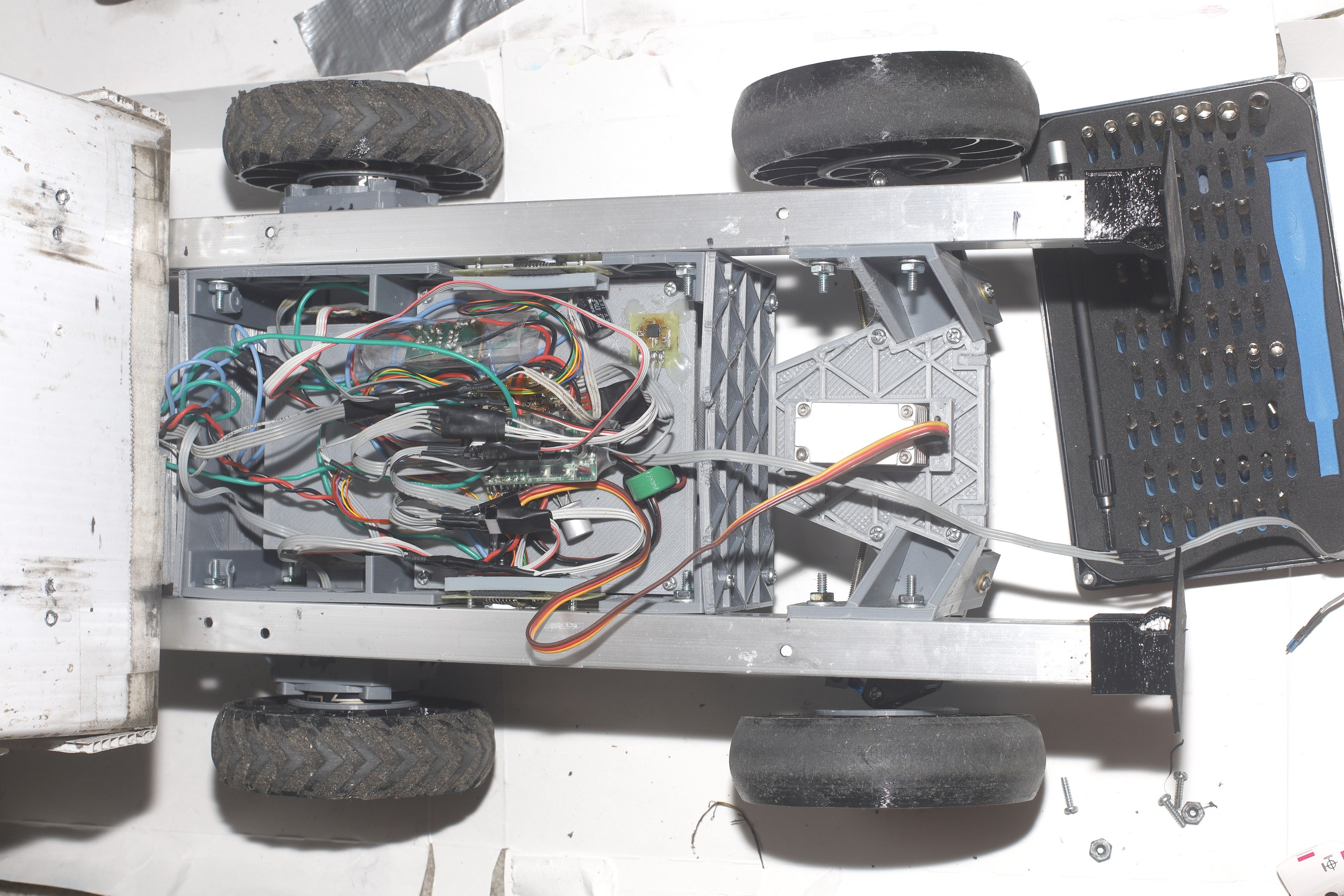
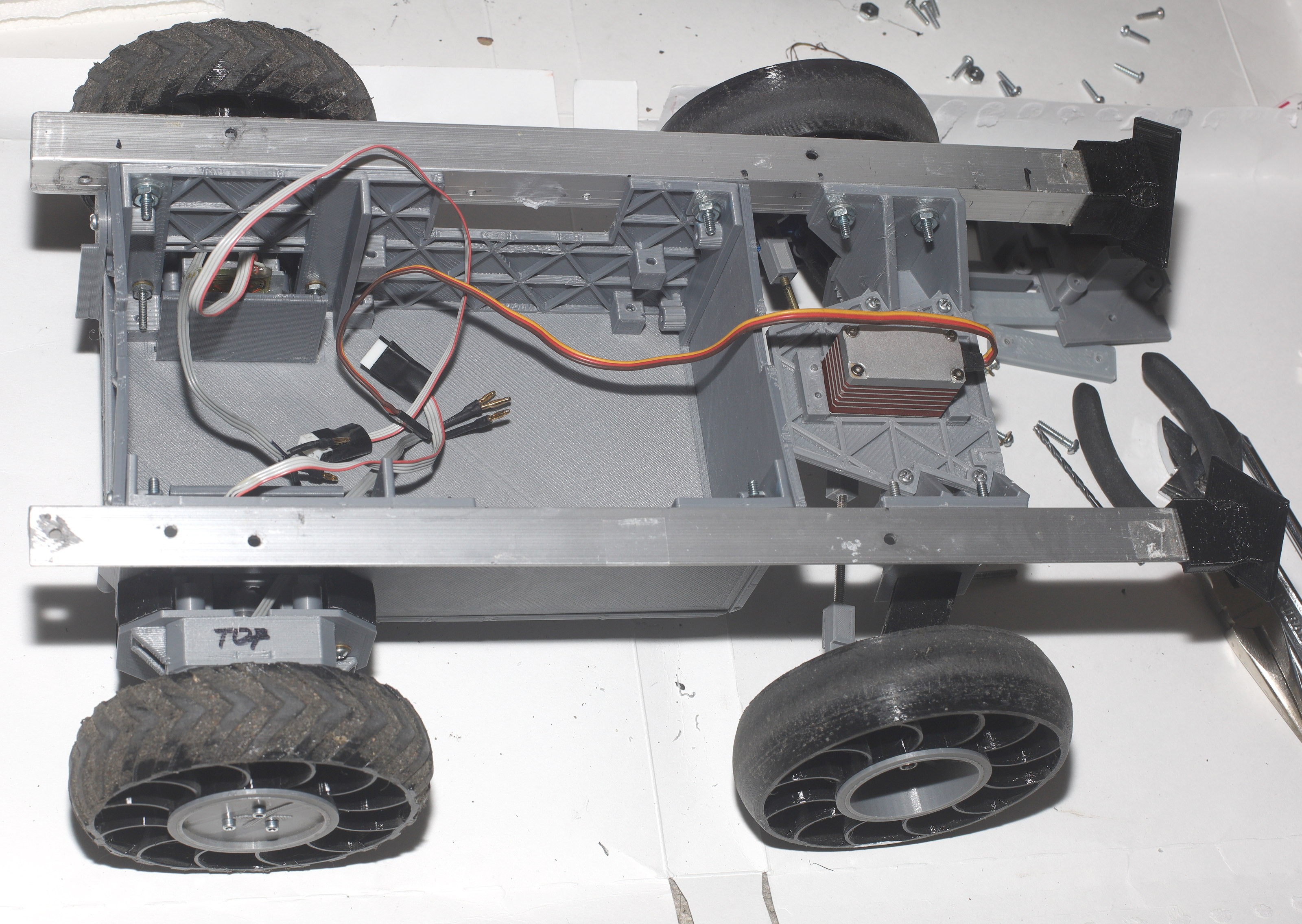
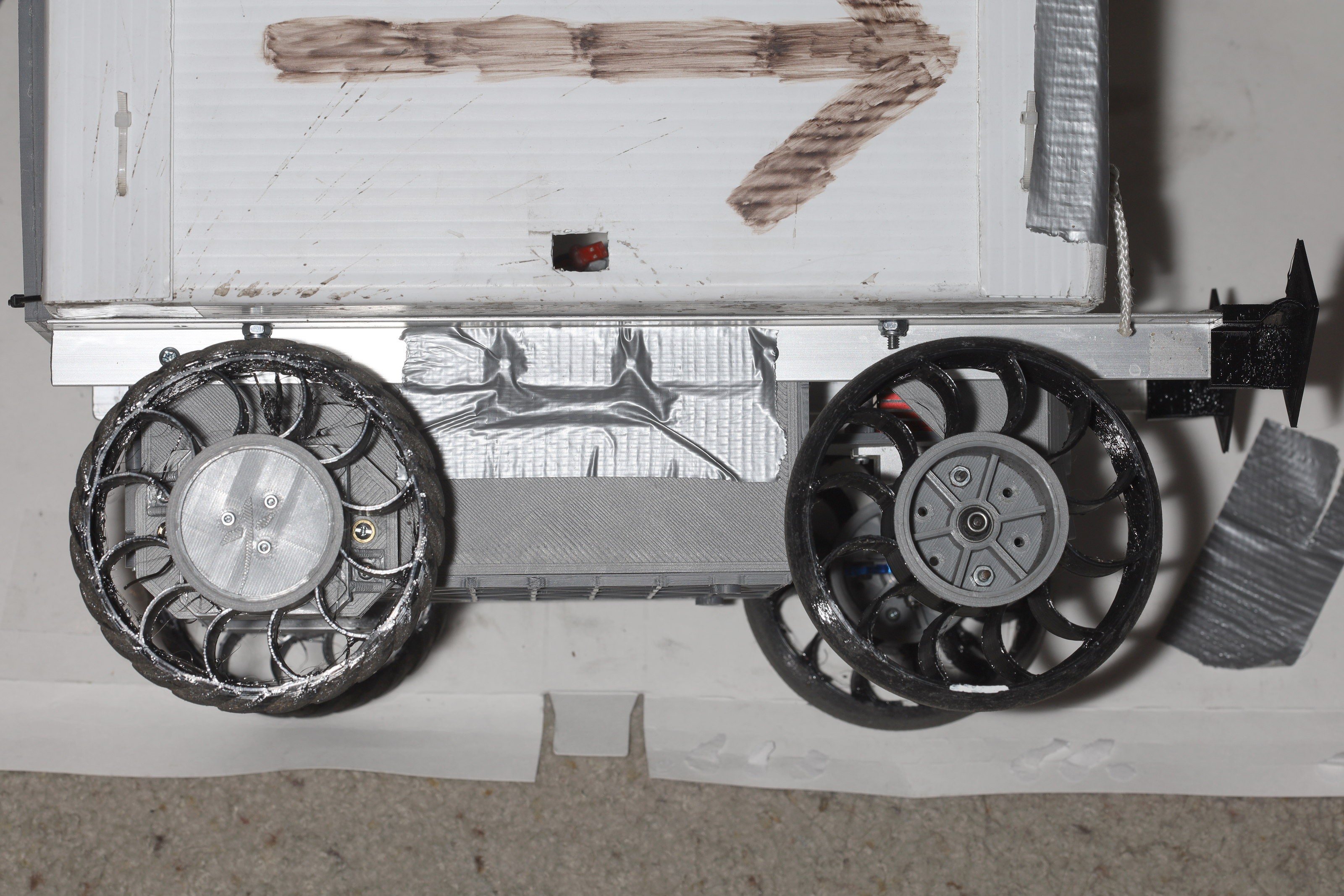
The easiest way to cover the H bridges was duct tape.
Torque limitations continued to plague the motors. It turns out the cheapest source of large diameter motors for this task is inside hoverboards. They're far cheaper than hobby motors of the same size. They're sealed from rocks. Hoverboards have long ago faded from popularity & their cheap motors might be going away. The motors replacing them are much smaller skateboard motors, with much less torque, at a much higher price.
The media was focused on the batteries in hoverboards, so the public became singularly focused on tearing down just the batteries while ignoring the motors. There are very few teardowns of the motors.
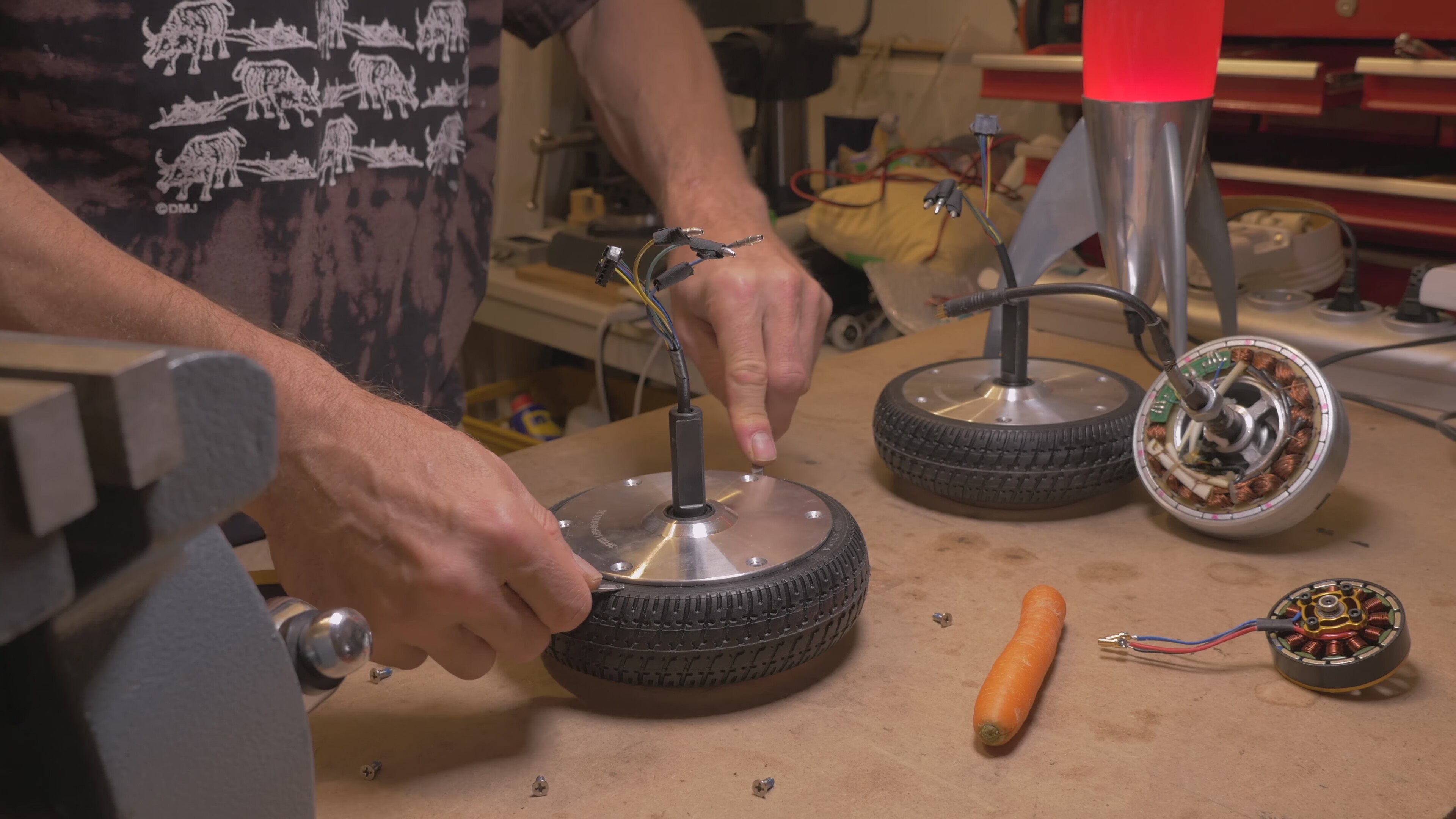
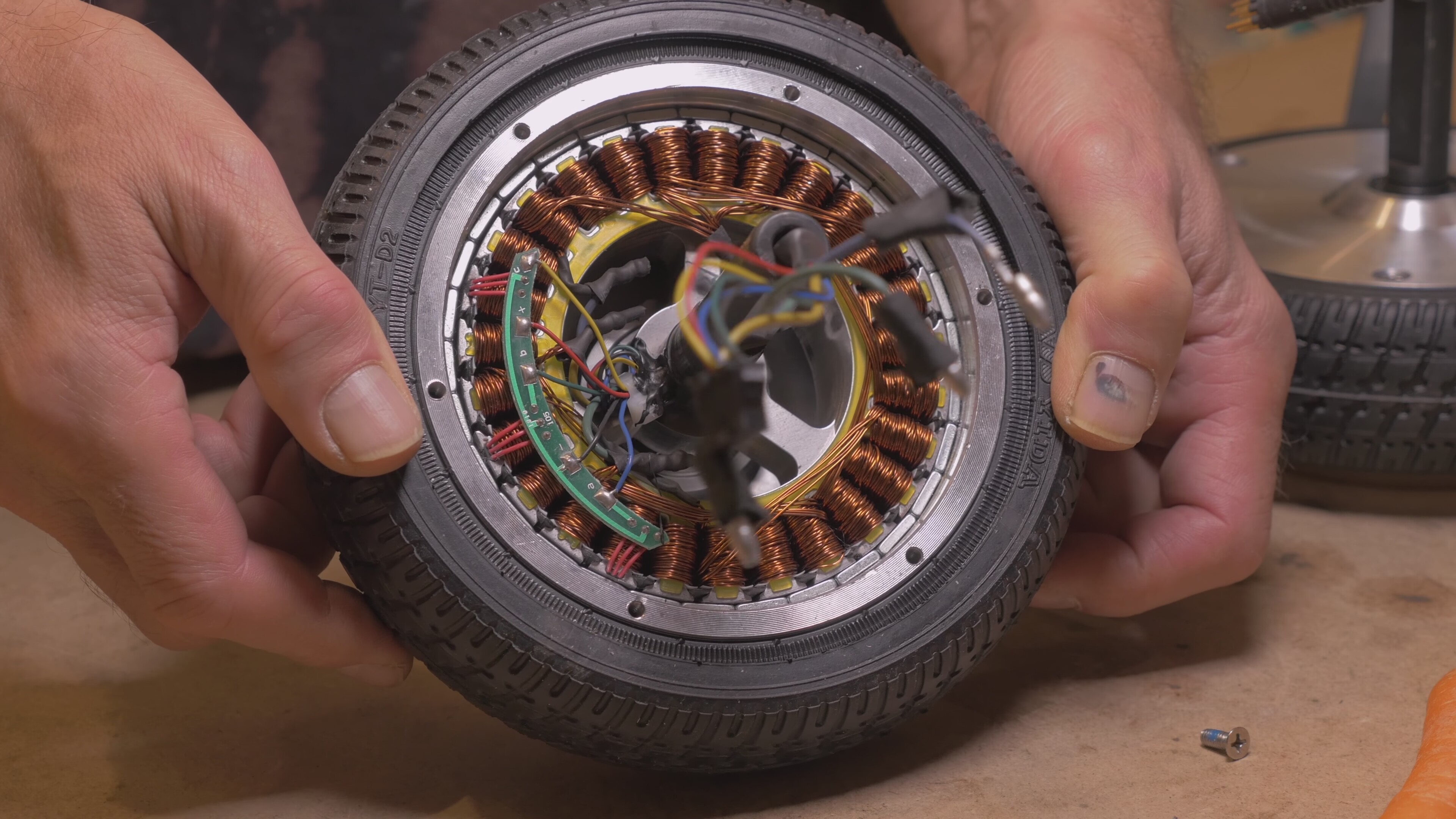
These are sadly too big for the truck in mind. They're too big even for a brushless gimbal. It's remarkable how economies of scale during the height of the hoverboard craze made such large motors almost free, while tiny hobby motors are a fortune.
Discussions
Become a Hackaday.io Member
Create an account to leave a comment. Already have an account? Log In.