The high cost of good RC truck kits, diminishing need for such kits & the noise of gearboxes made lions look elsewhere for a robot platform. 3D printing a truck from scratch, with only a few metal parts still being off the shelf, was the next step. The only parts which have to be outsourced are the motors, steering servo, & steering knuckles. Everything else is 3D printed, made of coroplastic, or home made electronicals. The size was based on the original Tamiya lunchbox.
Motors:
Motor numbers are comprised by their diameter & length, so a 4248 has a 42mm diameter & 48mm length.
The current ship has a Propdrive 4248 of any KV rewound with 20 turns of 26AWG according to the diagram. It doesn't produce enough torque to go up hills.
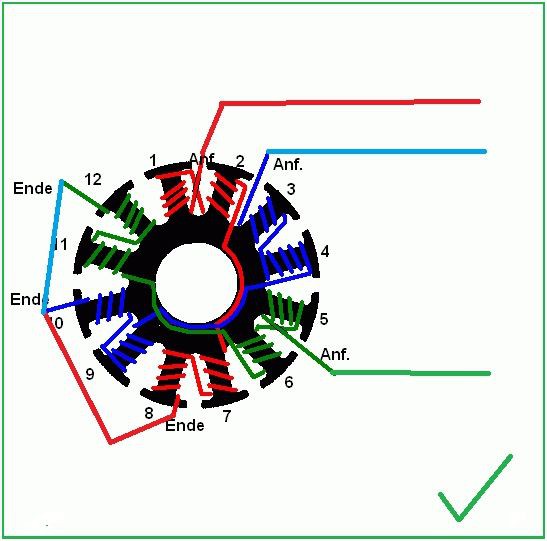
A Propdrive 5060 with lower AWG & more turns would be a better match.
Steering knuckles:
These have to match the wheel base, to achieve ackerman steering. Lions use
Jazrider Aluminum Front Steering Knuckle Upright For Tamiya RC CW01/Lunch Box
from fleebay & size the wheel base to within 1" of a lunchbox.
Steering servo:
The lion kingdom uses discontinued trackstar brushless servos with servo savers. Brushless is required to get any life out of them.
The 3 mane components are the steering module, traction module, & the coroplastic container. They're held together by aluminum angle rods.
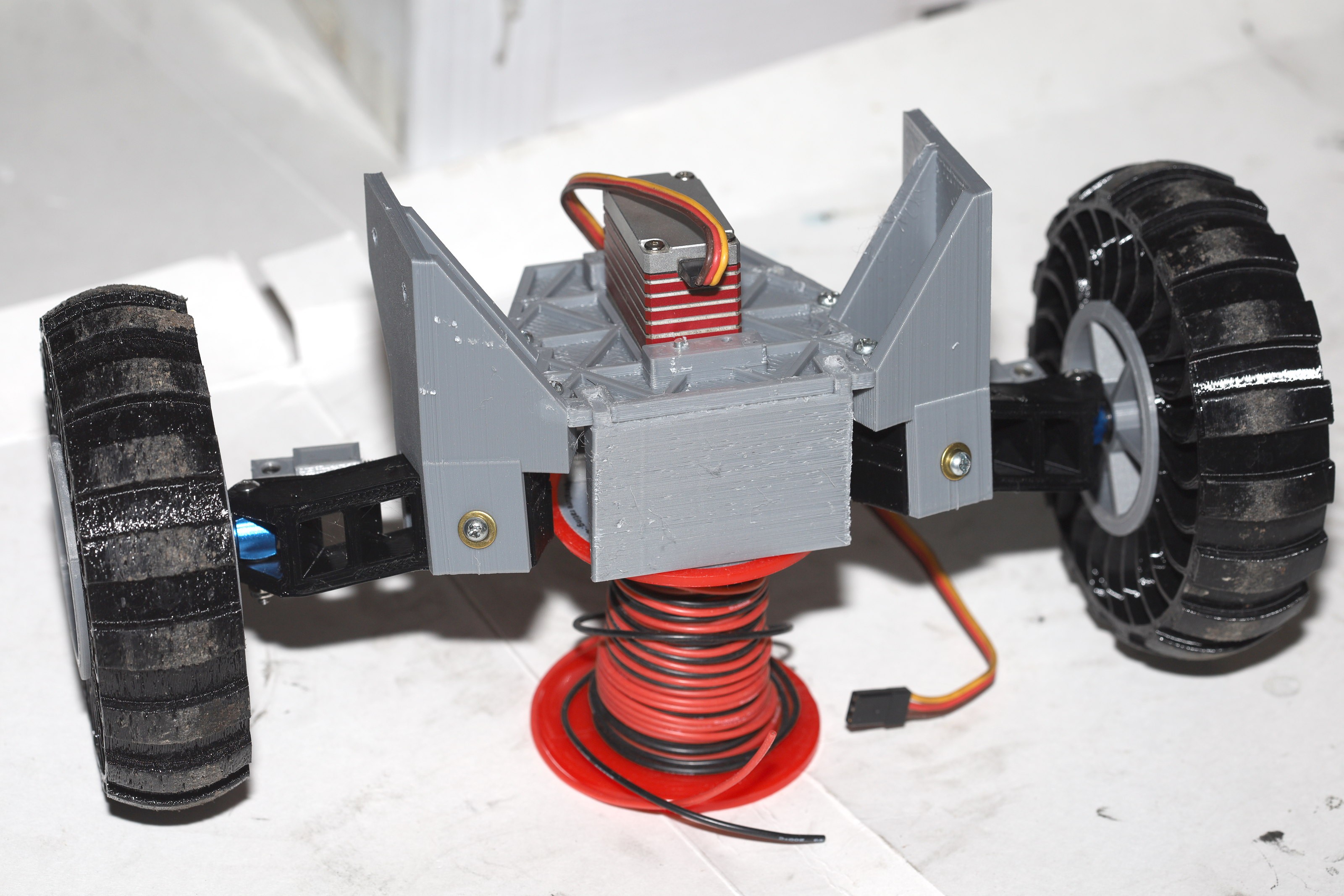
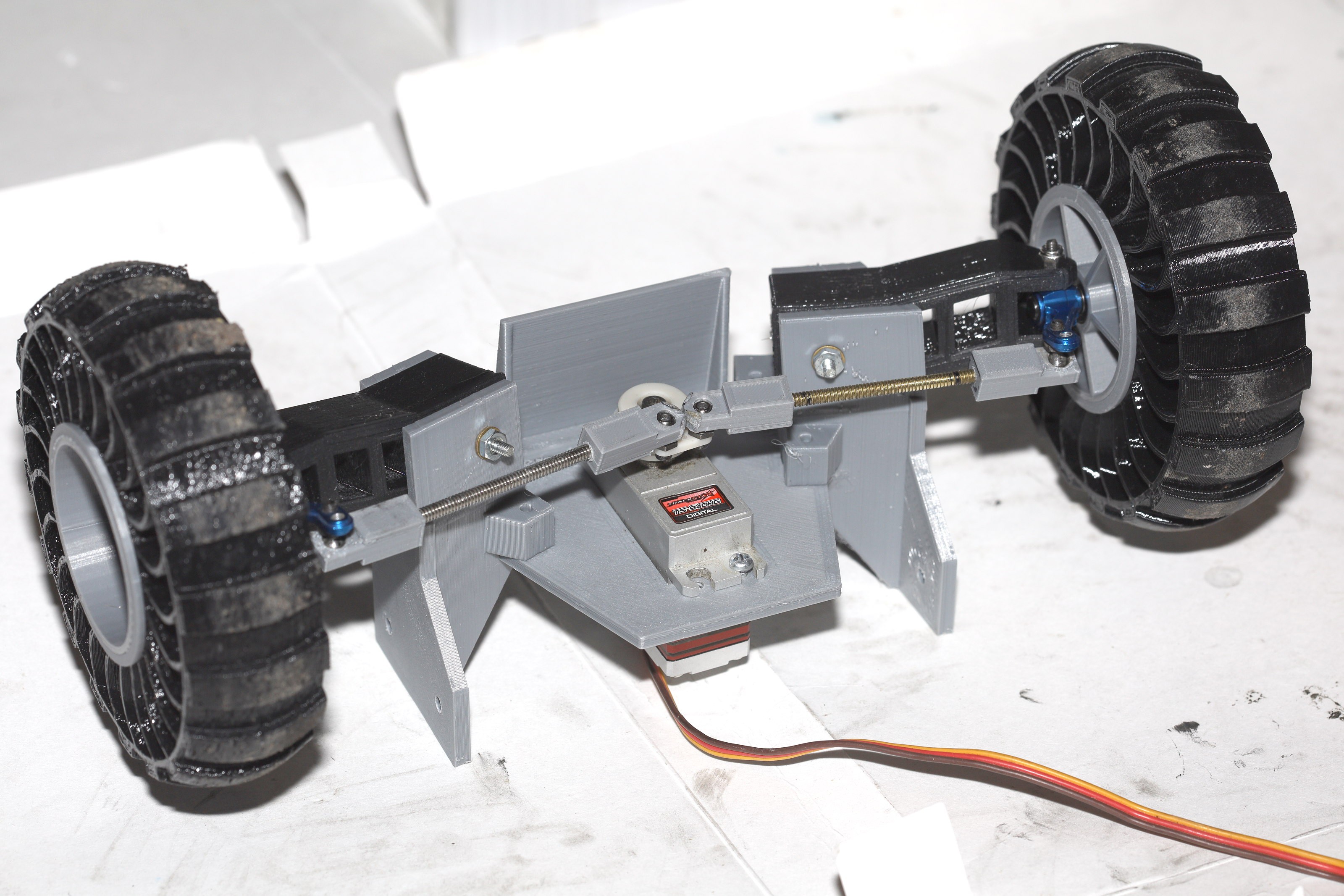
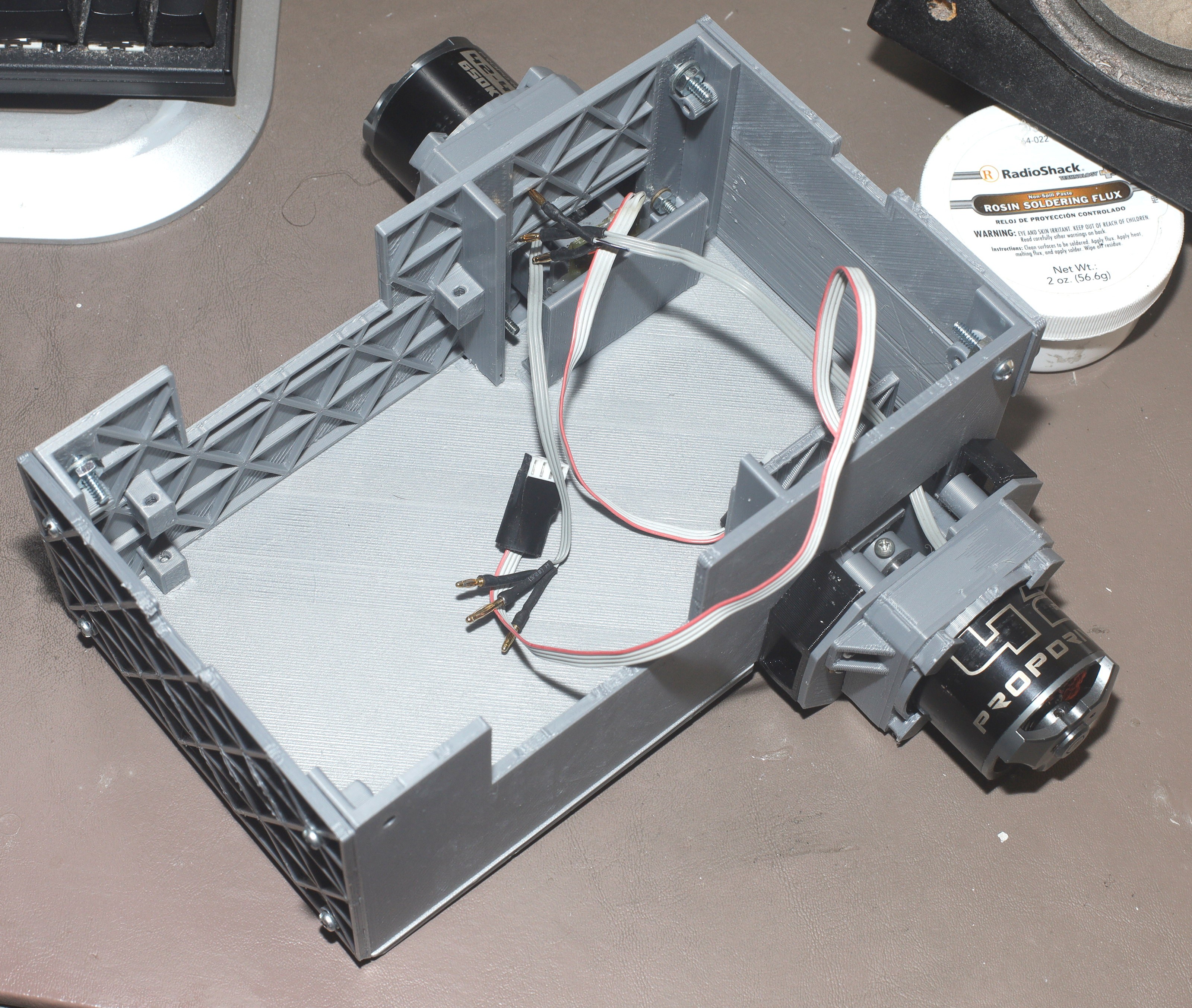
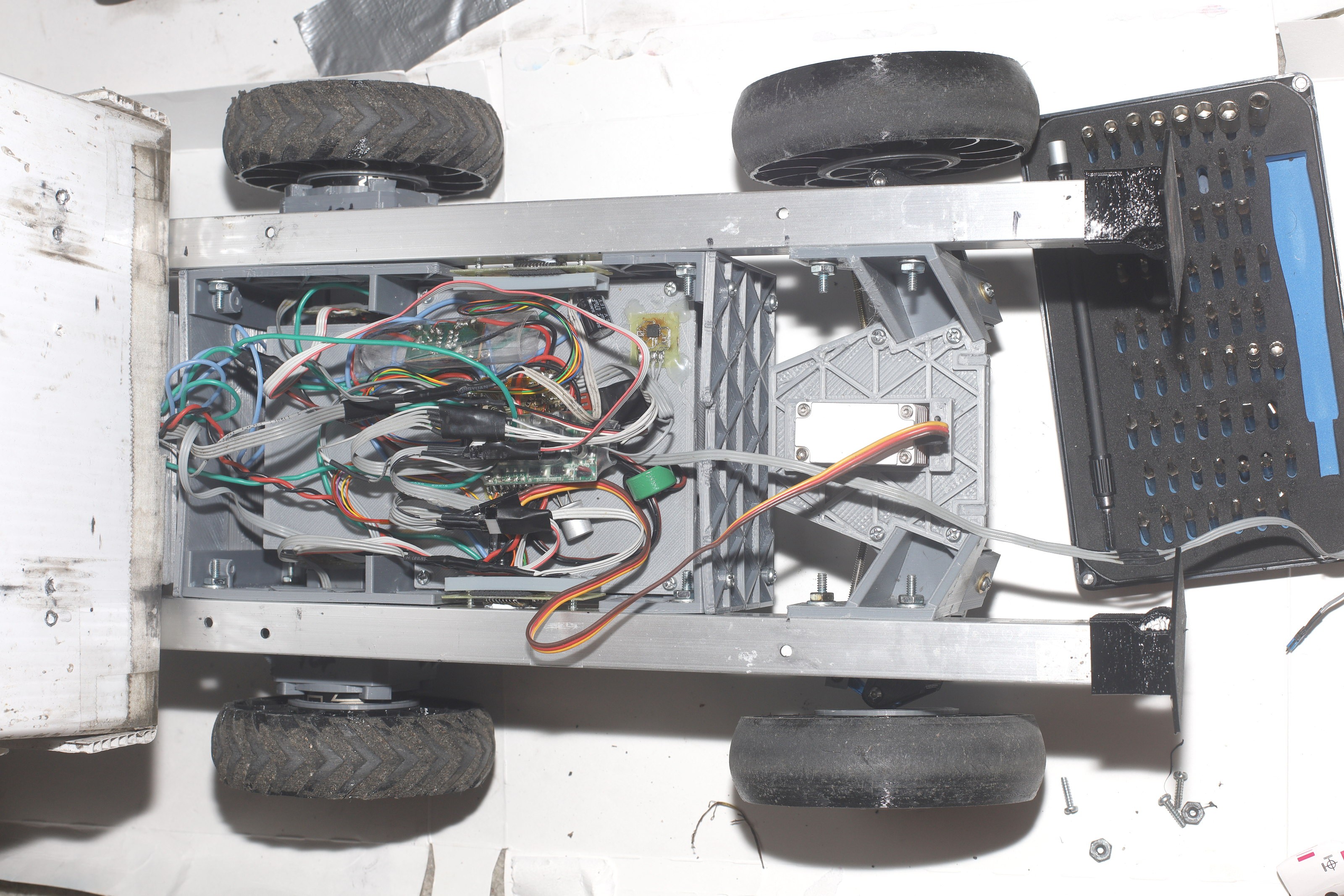
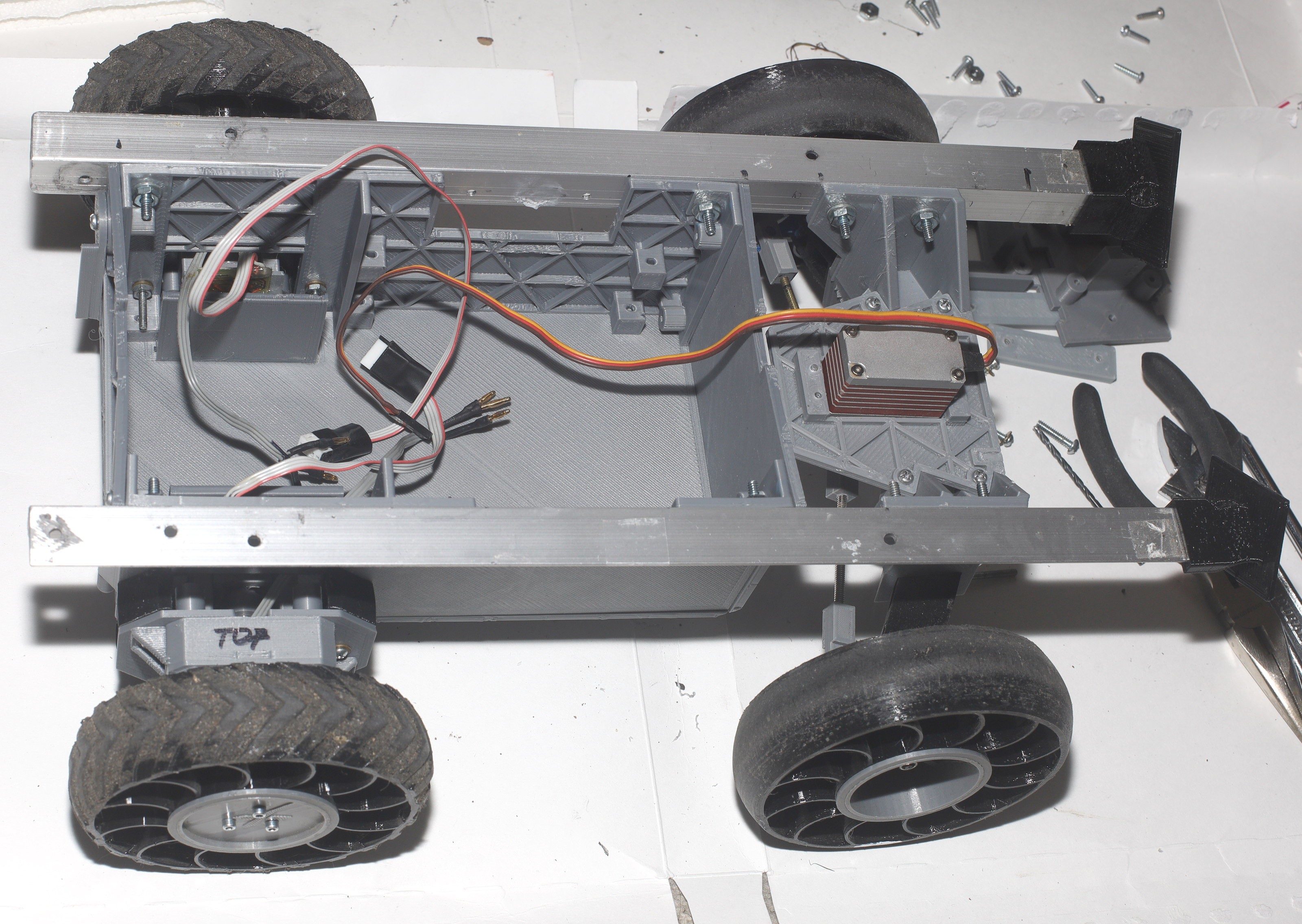
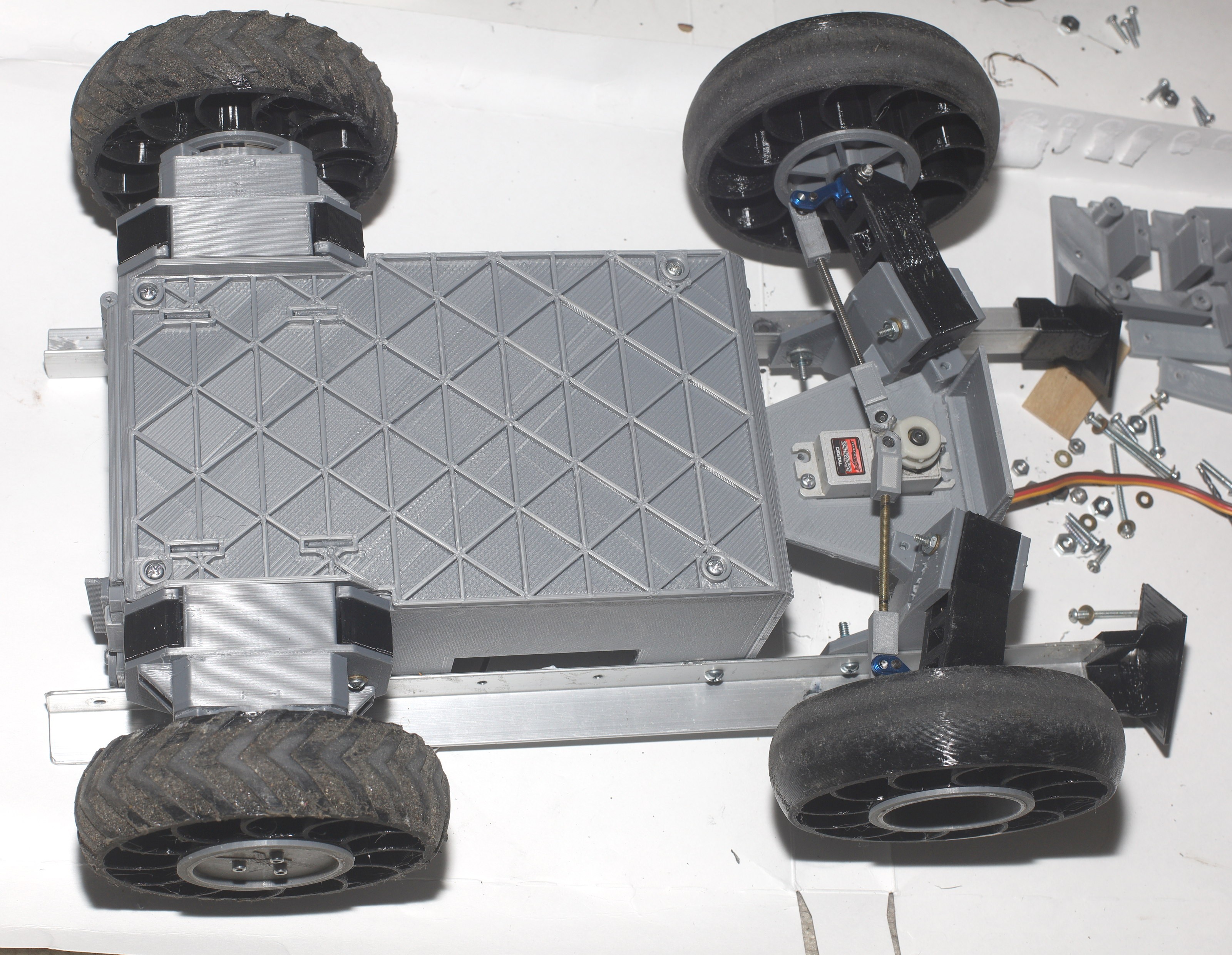
The tires are 3D printed out of TPU for a lot less money than Chinese ones.
The final mechanical piece is the paw controller. It uses springs from ball point pens.
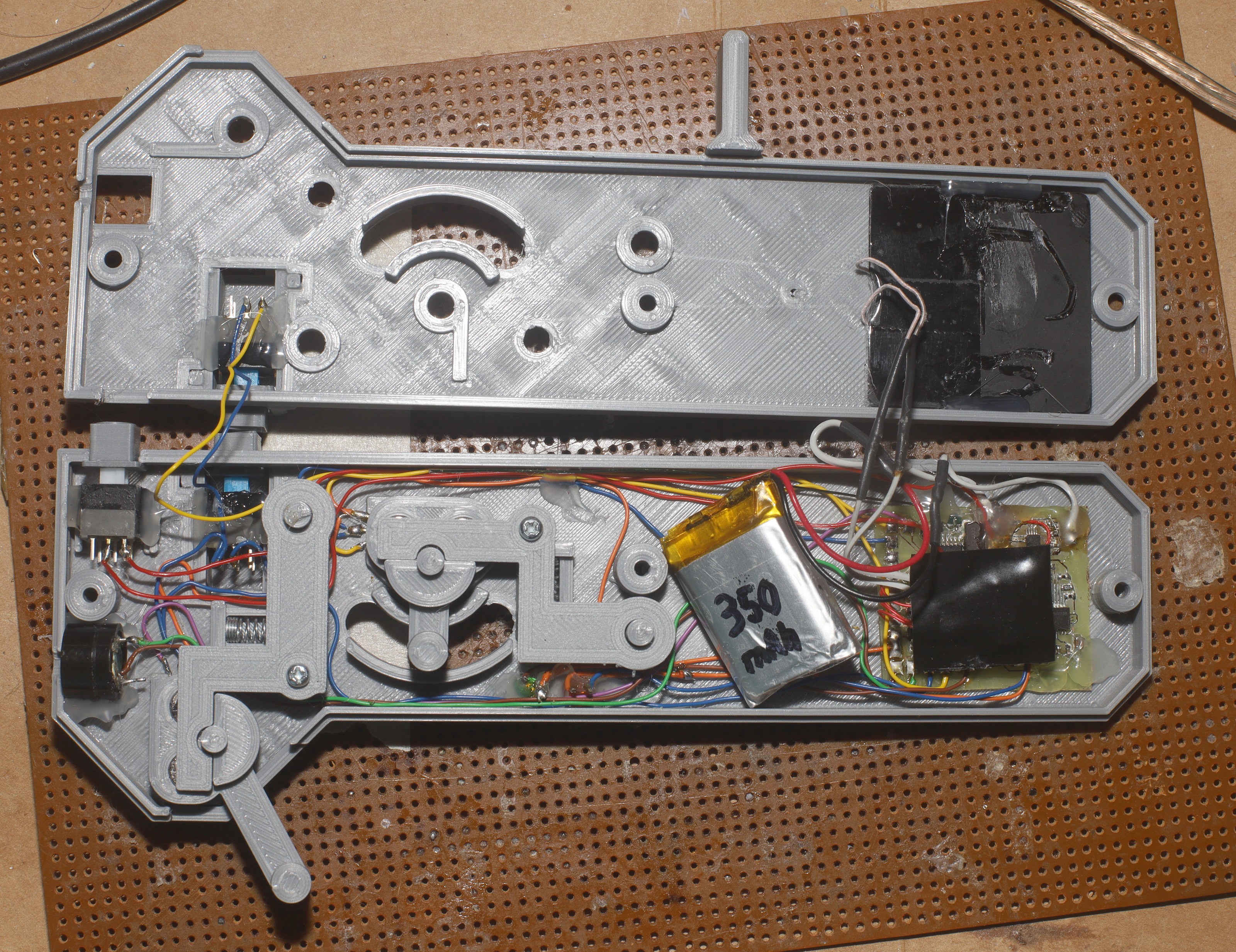
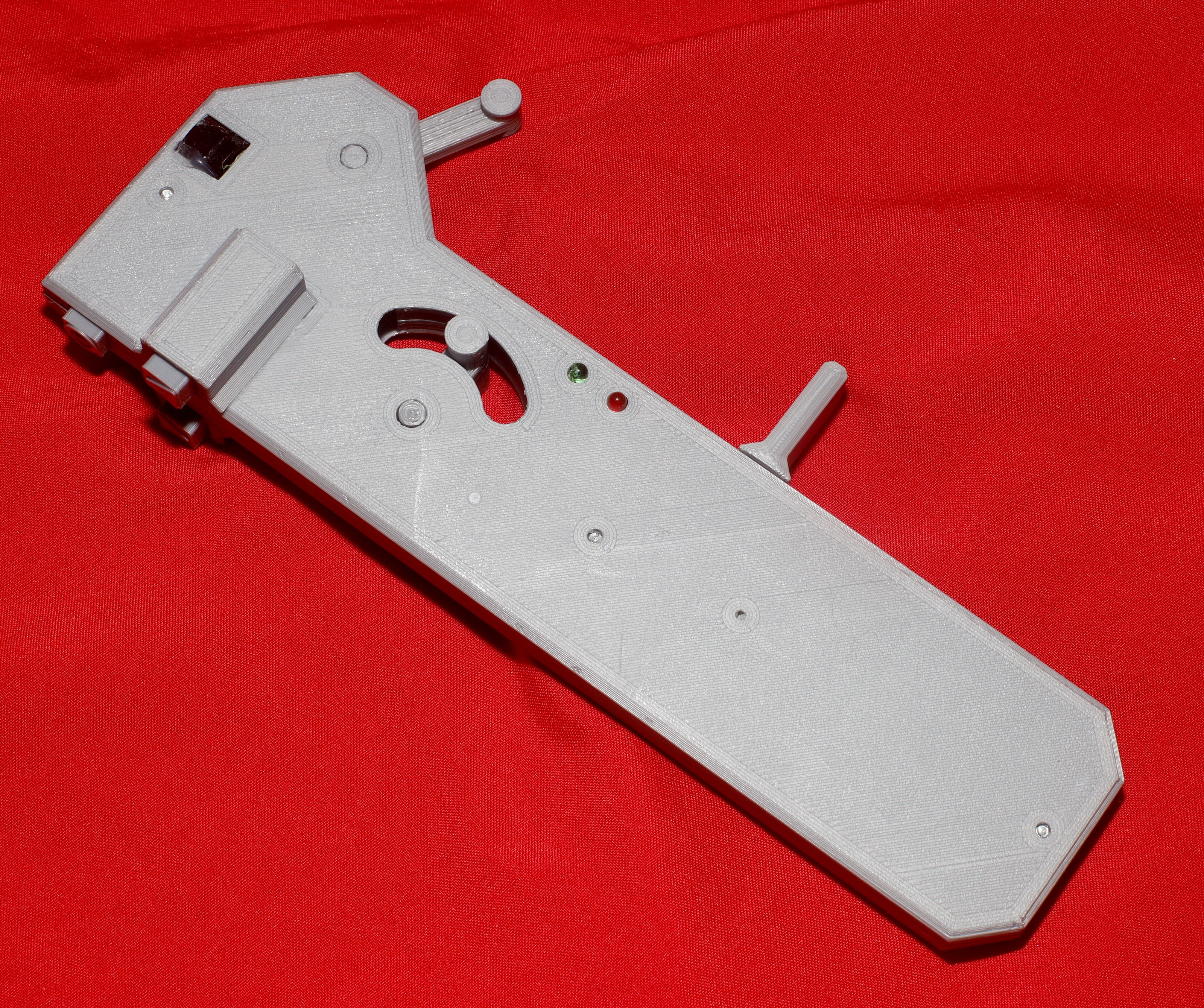
Electronicals provide semi autonomous throttle & steering.
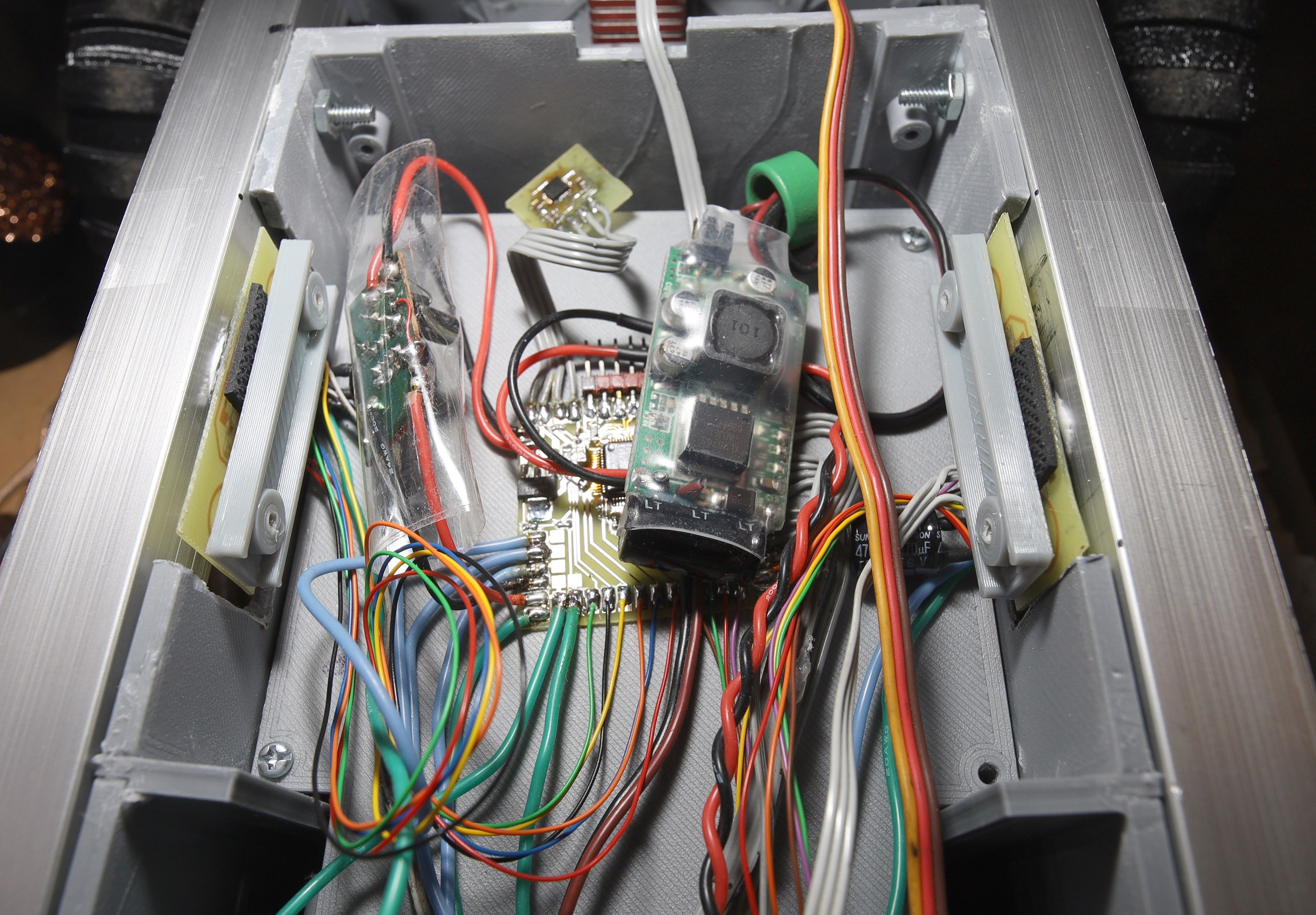
Hey! This looks like a neat project, as well as your running aid. Does that auto-follow? If so, how did you implement that?
I plan to one day produce a 'cycling aid', along the same lines, with enough of a payload (>20kg) to be useful on grocery runs. Do you think your printed truck would be a suitable RC vehicle for this? Or perhaps a starting point? I'd be after a vehicle that can keep up with, brake faster than, and handle the kind of terrain a bicycle can.